Table of Content
Integrity, sustainability, and innovation form the foundation of the steel industry, which plays a vital role in driving economic growth, creating employment opportunities, and promoting green and sustainable initiatives in the world.
It remains a source of pride for its global workforce, thanks to the industry’s commitment to employee development and safety, which has enabled it to employ millions of people. Besides, steel companies contribute significantly to local communities, providing essential infrastructure and ensuring financial growth.
Given its vital role in sectors like construction, automotive, and renewable energy, it is no surprise that steel consumption will rise by more than a third by 2050 despite declining by 2.3% in 2022 and rebounding by 1% in 2023, underscoring its relevance as an indispensable material.
The housing and construction sectors are the primary consumers of steel, representing over 50% of total steel production. Steel boasts the highest global recycling rate (60%), with around 680 million metric tons recycled in 2021 alone.
Future-forge: Unleashing the steel industry’s soaring potential
Many factors, including infrastructure development, urbanization, and technological advancements, influence its expansion - despite the recent impacts of the Ukraine-Russia war and China’s ailing real estate sector due to its extensive strict COVID lockdown policies.
But that has not stopped other countries from investing in transportation, energy, and construction, which is why the need for steel will also increase, especially in developing nations, where urbanization is rapidly progressing and the growth of middle-class populations means greater consumption of goods that rely on steel.
Secondly, the transition to renewable energy, electric vehicles, and more energy-efficient buildings requires substantial steel for construction and manufacturing.
Finally, technological advancements, including the integration of the Internet of Things (IoT), AI, and automation, have the potential to improve the steel industry’s efficiency, quality, and sustainability and open up new opportunities for OEMs to develop advanced steel solutions.
The adoption of Industry 4.0 technologies is poised to enable steel manufacturing to remain competitive and keep pace with the constantly evolving demands of modern infrastructure.
Enhance Your Steel Production Efficiency with Custom IoT Integration!
Explore ServicesCommon challenges faced by the steel industry OEMs
Steel, a cornerstone of modern civilization, indeed plays a vital role in shaping our world through its versatile applications. However, the industry OEMs face numerous challenges threatening their long-term viability and environmental impact. Let us take a look:
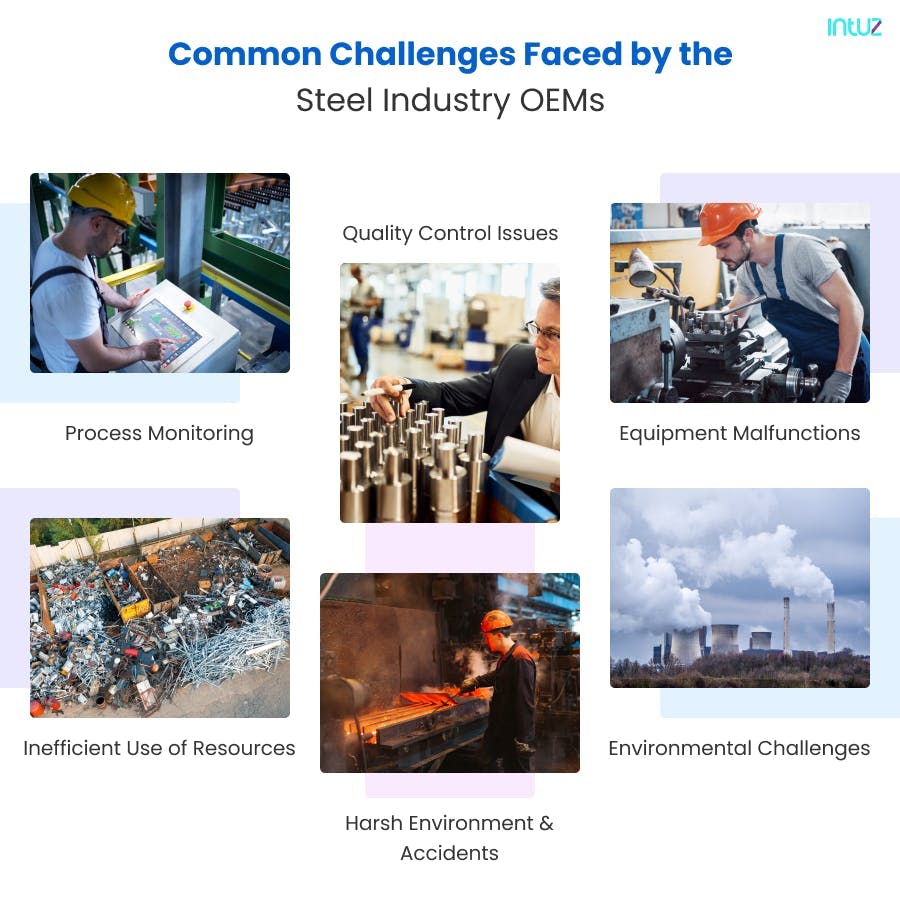
1. Process monitoring
Steel production comprises multiple stages, from raw materials to finished products. However, the lack of tracking and recording of these stages causes inefficiencies and quality issues. For instance, without proper monitoring, it can be difficult for OEMs to identify and address issues during production, resulting in delays, rework, and increased costs.
2. Quality control issues
Many parameters, such as temperature and humidity, must be closely tracked and analyzed by OEMs to ensure consistent quality when manufacturing steel. Failure to do so can lead to defects, cracks, and other issues, which hamper the final product’s performance and durability.
3. Equipment malfunctions
Steel manufacturers operate large and complex equipment, such as blast furnaces, rolling mills, and converters, which require regular maintenance and repair to ensure smooth operation. If OEMs fail to consider this aspect during production, they risk facing unplanned downtime, decreased worker productivity, and increased costs.
4. Environmental challenge
Despite steel being incredibly eco-friendly, it is a massive contributor to environmental pollution, emitting pollutants such as carbon dioxide (CO2), sulfur dioxide (SO2), nitrogen oxides (NOx), and particulate matter. These emissions have detrimental effects on the planet and human health, contributing to climate change, air pollution, and respiratory illnesses.
Smart Manufacturing With IoT: Benefits And Barriers of The Chemical Industry
Learn More5. Inefficient use of resources
The steel production processes require a significant amount of energy, oxygen, and raw materials. However, if OEMs fail to maintain and optimize their equipment regularly, these resources may be wasted, resulting in increased business expenses and decreased efficiency.
6. Harsh environment and accidents
Steel’s reliance on high-temperature thermal and chemical processes creates a hazardous work environment for operators. Preventing unexpected accidents in such scenarios is difficult, and inspecting and maintaining machinery and structures is also challenging due to corrosion and wear and tear. In addition, workers often act without knowing the real priorities within the operation, making the work environment stressful and unsafe.
How IoT solutions alleviate the pain points of the steel industry OEMs
Despite the challenges, the steel industry is well-positioned to capitalize on the opportunities ahead and achieve significant growth in the coming years because of IoT. Technology has transformed industries worldwide, and the steel manufacturing sector is no exception.
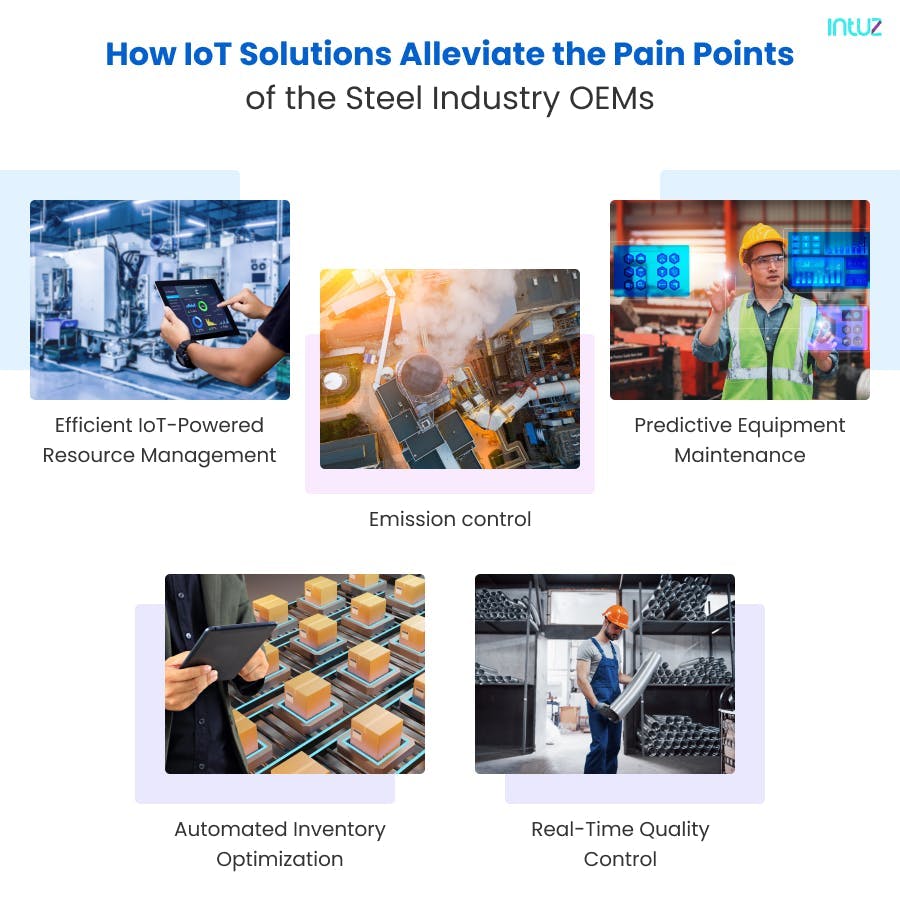
By integrating industrial IoT sensors and data analytics into various aspects of steel production, OEMs can significantly improve efficiency, product quality, and sustainability. Let us take a look at how they truly benefit from IoT:
1. Efficient IoT-powered resource management
Using IoT sensors, the steel manufacturing plant can collect real-time data on energy usage, which can be used to identify areas of inefficiency and take corrective action. For example, they can detect when the equipment consumes more energy than necessary, and the OEMs can adjust settings or schedule maintenance to optimize energy consumption.
In addition, these IoT solutions enable smart metering and billing, which help reduce operational costs and waste. By monitoring energy demand and supply, OEMs can adjust their production schedules to avoid energy spikes and reduce the need for energy storage.
2. Automated inventory optimization
By collecting data on inventory, throughput, yield, and other KPIs, IoT sensors can offer valuable insights into the steel manufacturing process and identify areas for optimization.
For example, with real-time data on inventory levels, the IoT solution for steel production management can automate the ordering of raw materials like iron ore, coal, and limestone, reducing the risk of stockouts or overstocking.
In addition, the sensors can track the movement of raw materials and finished products throughout the plant, providing real-time visibility into the production process.
3. Predictive equipment maintenance
IoT sensors are transforming how steel manufacturers operate by detecting and diagnosing equipment failures, breakdowns, and maintenance requirements.
By collecting and analyzing performance, condition, and usage data, these advanced sensors can effectively predict when machinery like blast furnaces needs maintenance or repairs, ensuring optimal performance and productivity.
This allows OEMs to address potential issues proactively, reducing the likelihood of unexpected breakdowns and unplanned downtime, which can be costly and disruptive to operations.
Moreover, IoT sensors can empower steel manufacturers to schedule servicing during periods of low demand or planned downtime. This strategic maintenance approach enhances overall efficiency and extends critical machinery's lifespan, reducing the need for frequent replacements and lowering long-term costs.
Customized Industrial IoT solutions. Get in touch!
Learn More4. Real-time quality control
IoT sensors can measure various parameters such as temperature, pressure, humidity, and so on that affect the quality of steel products. In a steel plant, they can track different stages of production and ensure consistent quality.
For instance, IoT sensors can monitor the temperature of molten steel during the casting process and provide feedback to the control system. If the temperature is too high or too low, it can result in defects such as cracks, voids, or surface imperfections.
Similarly, if the humidity is too high, it can cause corrosion or rusting of the steel surface. Upon being intimated, the control system can adjust the temperature or humidity levels to ensure that it is within the desired range, thus ensuring that the finished product meets the required quality standards.
5. Emission control
In today’s rapidly evolving industrial landscape, IoT sensors have emerged as crucial tools in mitigating the environmental impact of various industries, including steel manufacturing. They can accurately measure and monitor emissions of pollutants, such as CO2, SO2, NOx, and other harmful substances that affect the environment and human health.
Embracing the emerging technology not only aids the steel industry OEMs in controlling and reducing emissions but also plays a pivotal role in meeting regulatory compliance requirements. By integrating IoT sensors into production, steel plants can closely monitor pollutant levels and implement effective measures to curb their release.
One such measure is carbon capture and storage (CCS), which involves trapping CO2 emissions at their source and storing them safely underground, preventing their release into the atmosphere. The IoT solution for steel production can monitor emissions in real time, allowing OEMs to optimize the capture and storage process, reducing CO2 output and operational costs.
In addition to CCS, IoT sensors can assist in waste management and resource utilization, further reducing steel production's overall environmental impact. They can track and optimize material usage and waste generation, promoting recycling and repurposing within the steel manufacturing plant.
Let's Modernize Your Steel Production Line with IoT!
Contact UsOver to you
In conclusion, integrating IoT technology in steel manufacturing has the potential to bring about a revolution in the industry, with significant improvements in quality control, predictive maintenance, and inventory automation.
As the IoT landscape continues to evolve, we can expect further advancements and innovations in the steel industry, which will reshape production processes and pave the way toward a more sustainable and efficient future.
If you want to know more about integrating IoT technology into your manufacturing processes, book a free consultation today!