Table of Content
In the past five years, IoT has profoundly affected the manufacturing domain — from making warehouse operations more efficient to better-managing asset performance to optimizing supply chain logistics.
The technology allows manufacturing companies to plan, control, integrate, and exquisitely analyze processes by creating a network of connected systems, devices, machinery and equipment, and human beings.
Predictive maintenance, more specifically, has enabled manufacturers to enjoy ample opportunities in the guise of robust supply chains and the optimal use of machines.
The evolution of maintenance
Maintenance as a corporate practice has evolved in the past five decades. It is not just a domain of trades-people anymore. Engineers and architects see maintenance as a vital part of business operations because it positively impacts corporate profitability.
Earlier, manufacturers would consider the age of machinery as the factor for scheduling maintenance jobs. The older the equipment, the more frequently it would need to be maintained. According to the ARC Advisory Group, only 18% of equipment fails due to age, while 82% of failures occur randomly.
You see, maintenance used to be reactive to breakdown. However, now it is so much more proactive. Today, using IoT sensors and actuators means manufacturing companies can determine the equipment condition and accurately predict when a failure might occur.
Such foresight eliminates unplanned downtime and hefty costs, enhancing user experiences. Equipment gets maintained regardless of the actual need.
What is IoT predictive maintenance?
IoT predictive maintenance leverages the power of connected sensors and advanced analytics to revolutionize equipment upkeep. By continuously monitoring machine health through vibration, temperature, pressure, and other sensors, IoT systems collect vast amounts of real-time data. This data is then analyzed using sophisticated algorithms and machine learning models to detect subtle patterns and anomalies that might indicate impending failures.
The magic of predictive maintenance lies in its ability to forecast issues before they cause breakdowns. Instead of relying on scheduled maintenance or waiting for equipment to fail, organizations can intervene at the optimal time, maximizing uptime and minimizing costs. This proactive approach not only reduces unexpected downtime but also extends equipment lifespan and optimizes maintenance resources.
In practice, IoT predictive maintenance can transform industries. Imagine a factory where machines self-diagnose issues, automatically schedule maintenance, and even order their replacement parts. Or consider wind turbines that adjust their operations based on predicted weather patterns and their wear patterns. The potential for increased efficiency and reduced operational costs is enormous. Now let's understand what is industrial IoT predictive maintenance.
What is industrial IoT(IIoT) predictive maintenance?
Industrial IoT predictive maintenance uses smart sensors and data analysis to foresee equipment failures before they happen. For example, in a steel mill, vibration sensors on a rolling mill might detect subtle changes in the machine's operation. This data is sent through an industrial IoT gateway to a cloud platform, where advanced algorithms analyze it.
The system might notice that the vibration pattern is similar to what preceded a bearing failure in the past. It then alerts maintenance staff, suggesting they replace the bearing during the next planned downtime, rather than waiting for a catastrophic failure that could halt production for days.
This approach not only prevents unplanned shutdowns but also extends equipment life and optimizes maintenance schedules. It transforms maintenance from a reactive necessity to a proactive strategy, significantly improving efficiency and reducing costs in industrial operations.
Optimize Your Industrial Equipments Maintenance with IoT Predictive Solutions
Explore NowPreventive vs. predictive maintenance
Both of these maintenance types aim to increase uptime and reduce unplanned downtime. The major difference between the two comes in timing and the ability to predict the future condition of an asset.
Preventive maintenance uses historical data to anticipate the condition of an asset. There are regular maintenance schedules in place. This may be good from a planning perspective. However, it may not be able to encounter asset failures.
Predictive maintenance ensures the avoidance of unnecessary maintenance by carefully understanding the present condition of the asset. It can flag up and fix any problem much earlier than preventive maintenance. This ensures that more serious issues do not come through. Predictive maintenance uses cutting-edge technologies like artificial intelligence and the Internet of Things (IoT) to generate insights.
Within predictive maintenance, models created through algorithms are employed to anticipate potential future issues, thus minimizing the likelihood of the asset experiencing further breakdowns. This proactive approach can lead to decreased maintenance expenses, a significant reduction of approximately 35-50% in downtime, and an extended lifespan of assets by 20-40%.
In conclusion, despite having the same overall goals of improving asset reliability and reducing failures, preventive and predictive maintenance procedures are very different. While predictive maintenance focuses on timely and accurate information about assets, preventive maintenance adheres to a regular and routine plan. When there are few serious repercussions from failure, preventive maintenance is appropriate for assets with known failure patterns, such as recurring or regular problems.
Predictive maintenance, on the other hand, is more advantageous for strategic assets with unanticipated failures and significant economic consequences. By streamlining maintenance procedures and improving asset performance, the effective deployment of predictive maintenance solutions ultimately results in higher customer satisfaction and significant cost savings.
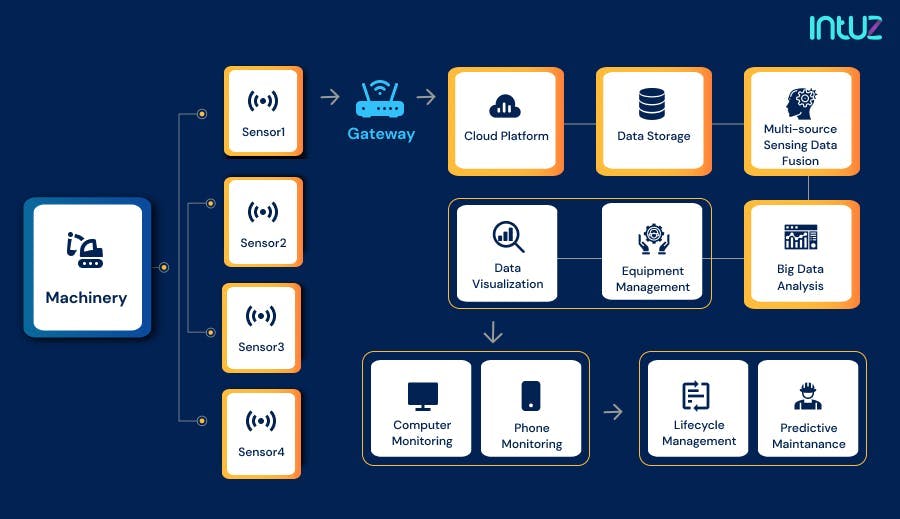
Explaining the role of IoT in predictive maintenance
You might be wondering what is the need for an Industrial IoT (IIoT) solution if there is SCADA, a control system architecture, for overseeing all forms of maintenance activities. Let us understand that in much greater detail.
Predictive maintenance can process large volumes of data and run sophisticated algorithms, which cannot be achieved by locally implementing SCADA.
To tap into the full mettle of IoT in predictive maintenance, think about the architecture and how it collects machine data (supply voltage, operating temperature, vibration) through sensors to wirelessly transmit gathered data to a cloud-based centralized storage facility in real-time.
An IoT-based software such as an intelligent factory app stores terabytes of data and runs machine learning algorithms on several computers parallelly for forecasting potential hazards and predicting timelines when industrial equipment can potentially fail.
Maintenance teams pull those data sets out of the storage and analyze them using AI and Big Data algorithms to derive actionable insights. They are incredible at finding patterns in enormous amounts of data.
However, this will only work if you have large volumes of updated and accurate inputs, where data-tracking IoT devices can make all the difference. They help manufacturers respond even faster to equipment issues.
IIoT is also reasonably user-friendly and modular. For example, air compressors form a standard part of industrial equipment. These devices pump high-pressure air, clean dust from sensitive equipment, refill gas cylinders, and power pneumatic instruments.
With the right tools such as controllers, input/output racks, simple sensors, and power supply transmitters, you can set up an IoT system capable of tracking variables vital to compressor functions like vibration, motor temperature, humidity, and dew point.
What is more — IIoT predictive maintenance systems are typically easy to scale up or modify. You can easily uninstall the IoT sensor and reinstall it where needed — for instance, extra pieces of equipment. The sensors will transmit data as they are supposed to.
Six benefits of IoT-based predictive maintenance
IoT predictive maintenance deploys the IoT technology to study a production system in real-time and forecast when and how a malfunction may occur in its component(s). In the following section, we will look at all the six benefits IoT predictive maintenance offers:
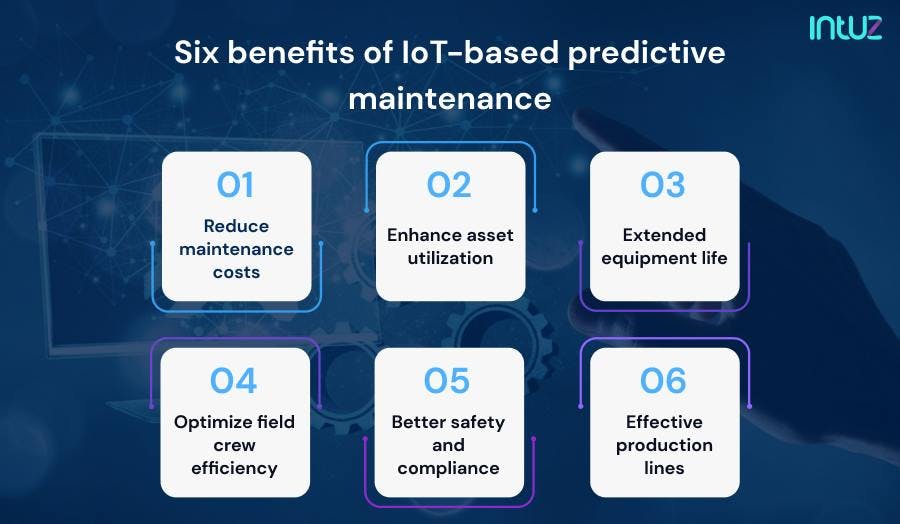
1. Reduce maintenance costs
Every asset has multiple associated costs. And if you add to that the expenses incurred because of an unexpected failure, that will significantly bump up the total cost of asset ownership. Therefore, companies can save money by predicting and avoiding equipment failure. In asset-intensive sectors, improving maintenance planning can lead to substantial cost savings.
IoT-based predictive maintenance makes use of historical data from various sources, including sensors and IoT devices, for forecasting asset health, equipment utilization, and the possibility of the future, enabling you to take a call based on the information, be it scheduling optimal maintenance or conducting routine inspections.
Reduce the amount of time the equipment is down for maintenance by making repairs beforehand. Enable smooth operations.
2. Enhance asset utilization
All manufacturers fear unplanned downtime because of equipment failure, expensive maintenance and repairs, and costs incurred due to production delays. Thankfully, IoT-based predictive maintenance enables more efficient utilization of assets.
The technology helps identify the causes of delay, whether they are external or internal, and set up processes to address the pain points.
IoT-based predictive maintenance detects operational issues before the equipment fully breaks down and gives early warnings, thus improving asset reliability and performance.
Top Databases In The Market For IoT Applications
Learn Now3. Extended equipment life
IoT-based predictive maintenance allows you to monitor, maintain, and optimize assets for more effective utilization, availability, and performance. Gain clearer visibility into how your equipment is performing via real-time monitoring.
Forecast machine failure and identify parts that need replacement. Schedule maintenance and repairs even before they occur and get real-time notifications to hit the ground running before any major malfunction happens and disrupts the overall operations.
4. Optimize field crew efficiency
IoT-based asset monitoring tools enable you to monitor field assets' health periodically. When a machine breaks down, the field crew must relocate to fix it on an ad-hoc basis. Moreover, they might need to hire extra personnel, depending on the damage done.
And if they do not have the equipment or experts to repair the machinery, they can also wholly reschedule other planned maintenance activities.
Predictive maintenance gives you a 360-degree view of asset health and helps you plan for the field crew beforehand. That reduces the response time and maintenance duration conveniently.
5. Better safety and compliance
IoT-based predictive maintenance helps companies anticipate and address possible safety risks and calculate potential issues before they start impacting workers. They can quickly take action to reduce safety risks via data analysis from multiple sources and the information generated from sensors and actuators.
By analyzing data over the longest periods, you can create a list of potentially hazardous conditions and estimate their impact on daily operations. A proper IoT-based predictive maintenance solution triggers instructions to reallocate resources and keep exposure levels below the threshold values, thus always complying with the regulations.
6. Effective production lines
With the capability to constantly monitor equipment performance, one can avoid unscheduled downtimes and improve overall operations throughput. This keeps the machinery's health in check and enhances production quality.
How does predictive maintenance work?
It categorizes the plant condition by checking them periodically (when offline) or consistently in real-time. In an ideal scenario, machine maintenance should be cost-effective and performance-oriented.
To keep operational disruptions to a minimum, you can conduct most predictive inspections online. Several machine components are assessed during maintenance, including vibration analysis, acoustics (ultrasound and partial discharge), infrared, and sound levels.
Of course, such test processes do not impair the machine's function, and operations can continue as usual. If you want to deploy predictive maintenance strategies in your manufacturing unit for the long haul, please follow the steps mentioned below:
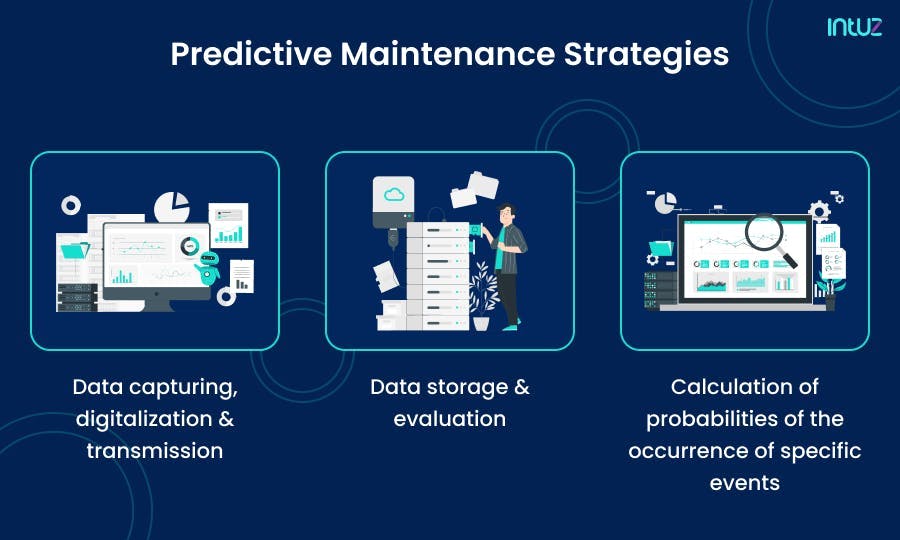
Data capturing, digitalization, and transmission
Data storage and evaluation
Calculation of probabilities of the occurrence of specific events
Widely used IoT sensors for predictive maintenance
IoT sensors for predictive maintenance are the eyes and ears of industrial systems, continuously monitoring equipment health. These sophisticated devices collect a wide range of data to detect early signs of wear, degradation, or impending failure. Here are some key types:
Vibration sensors
Essential for rotating machinery, they detect unusual vibrations that might indicate bearing wear, misalignment, or imbalance.
Temperature sensors
Monitor heat levels in equipment, alerting to overheating issues that could lead to failures.
Acoustic sensors
Listen for abnormal sounds in machinery, which can indicate problems like air leaks or faulty gears.
Pressure sensors
Track fluid or gas pressure in systems, crucial for detecting leaks or blockages.
Oil analysis sensor
Measure particle count and oil quality in real-time, signaling when lubrication is degrading.
Electrical current sensors
Monitor power consumption patterns, which can reveal motor issues or inefficiencies.
Humidity sensors
Important in environments where moisture can affect equipment performance or lifespan.
These sensors feed data to IoT gateways, enabling real-time analysis and predictive insights. By catching subtle changes early, they help prevent unexpected breakdowns and optimize maintenance schedules.
Key components of IoT-based predictive maintenance
With sensors gathering real-time data across various devices, systems, assets, and locations, IoT-based predictive maintenance enables manufacturers to effectively anticipate and plan for events such as equipment breakdown or parts replacement. Here are five components of an IoT-based predictive maintenance platform:
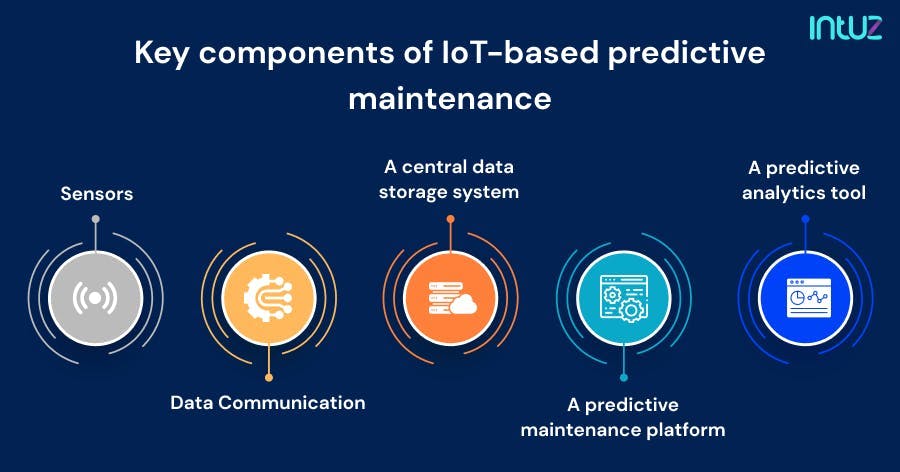
1. Sensors, which gather all the machine data by deploying them at specific points in assets.
2. Data communication, a system that allows data fetched from sensors to move to centralized data storage in the cloud.
3. A central data storage system, where all the equipment data and business information (coming from other IT systems) is safely stored.
4. A predictive maintenance platform, which streams all data sets to maintenance teams and repair engineers and notifies them when a machine operates beyond a user-defined range. It also fetches periodic reports for further analysis.
5. A predictive analytics tool that utilizes ML-based algorithms and analytics programs for generating actionable insights from data.
IoT predictive maintenance use cases for various industries
IoT predictive maintenance finds diverse applications across various industries, revolutionizing how equipment is managed and maintained. Here are some key industry applications and use cases:
Manufacturing
- Monitoring production line equipment to prevent unexpected shutdowns
- Predicting tool wear in CNC machines to optimize replacement schedules
- Analyzing robot performance to maintain precision and efficient
Energy and Utilities
- Monitoring wind turbine vibrations to predict gearbox failures
- Analyzing power transformer health to prevent grid outages
- Predicting pump failures in water treatment plants
Transportation
- Monitoring aircraft engine performance for proactive maintenance
- Predicting wear on train wheels and tracks to optimize replacement
- Analyzing fleet vehicle health to schedule preventive maintenance
Oil and Gas:
- Monitoring offshore drilling equipment to prevent costly downtime
- Predicting pipeline corrosion to prevent leaks and environmental damage
- Analyzing refinery equipment performance for optimal operation
Healthcare
- Monitoring MRI and CT scanners to prevent unexpected breakdowns
- Predicting maintenance needs for critical life support systems
- Analyzing laboratory equipment performance for consistent results
Agriculture
- Monitoring irrigation systems to predict pump failures
- Analyzing harvesting equipment to optimize maintenance during the off-season
- Predicting greenhouse climate control system failures
Mining
- Monitoring conveyor belt systems to predict failures
- Analyzing haul truck performance to optimize maintenance schedules
- Predicting drill rig component failures to minimize downtime
These applications demonstrate how IoT predictive maintenance can enhance efficiency, reduce costs, and improve safety across a wide range of industries.
Two ways to kickstart IoT-based predictive maintenance
If you have read this far, you will agree that the technology helps reduce asset downtime and unplanned maintenance routines. You are also equipped with the knowledge of the core components required for creating IoT-based predictive maintenance software solutions. Here is what you need to do to take a step further in that direction:
1. Identify assets that need predictive maintenance
Before you start deploying the technology in your manufacturing unit, you must know that not all machines will need predictive maintenance. To identify which ones would need it, think about the impact of minimal downtime of specific equipment on your bottom line.
Sort the identified assets based on their past downtime incidents and the business loss they can lead to. That way, you will know which ones to pick up on priority for predictive maintenance.
2. Choose the right software
With hundreds of systems available in the market, searching for the right predictive maintenance platform can be a bit challenging. You have to find the perfect fit because it is a costly investment, unlike purchasing clothes off the rack!
Speak to various vendors to get clarity about how their products can help. Schedule a demo or two. Ask if you can try a few features of their IoT-based predictive maintenance system for a defined timeline. While doing your research, check out user reviews about the IoT development company to get an idea of how their experience was.
IoT predictive maintenance examples
The technology has already been in use to a great extent in many manufacturing initiatives for developing smarter factories of the future. Sweden-based engineering company Sandvik, for instance, teamed up with Microsoft to create sensorized cutting equipment.
The technology combines streaming analytics, data collection, and machine learning algorithms to notify engineers when the tool bit maintenance is required or to offer an alert of impending failure. On the other hand, ABB, an engineering multinational specializing in robotics, has developed a predictive maintenance system for driving applications in manufacturing.
In this scenario, cloud computing, machine learning algorithms, and sensors combine to offer an overview of equipment performance for keeping the production running as planned. This has been beneficial for the Italian steel pipe manufacturer, Tenaris.
It uses predictive maintenance to track high and low-voltage motors operating critical fans and pumps 24/7. The system has been used for collecting and analyzing vibrations to highlight failure and any anomalies in power or voltage that indicate a short circuit.
Future of IoT predictive maintenance
Putting IoT predictive maintenance into practice can sound a little frightening at first. However, the key is to take baby steps to make the process easier. We recommend kickstarting a "pilot" asset to integrate with predictive maintenance tools and software.
By emphasizing just physical assets at a time can make your maintenance approach a little less overwhelming. That will also give you a better idea of whether IoT predictive maintenance is right for your business.
Even though the cloud computing technology supports predictive analytics systems, businesses can gain a crucial advantage by refining the data processing and analysis speed and performance by leveraging the edge computing technology.
A predictive maintenance system operating at the edge reduces data storage. It also minimizes costs thanks to low latency and real-time access to data analytics. When IoT solutions are implemented through cloud computing, vast data gets shared over the network to the cloud.
As the load on the internet continues to grow with each passing day, the cost of networking also increases. Predictive maintenance solutions analyze the data on the premises in real-time to shave off the amount of data shared on the cloud. This also reduces cloud storage costs.
Explore Industrial IoT Equipment Vibration Solution
Read NowOver to you
All manufacturers, big or small, require robust predictive maintenance strategies. The demand for increasingly complex yet comprehensive IoT solutions for the same will only grow over time.
As a manufacturing business at the forefront of software and hardware development, having robust technology is paramount. Cloud migration and the subsequent web app implementation are some of the most efficient ways to manage high-end predictive maintenance systems.
Otherwise, you might get down with a complex manual setup and might get bogged down to human factors. That is why you must find a reliable software developer who offers full-package solutions for large-scale manufacturing businesses.
The good news is the specialists at Intuz are ready to assist you with entering the predictive maintenance market and achieving your other goals by providing expert support on any IoT predictive maintenance-related matters.
Book a 45-minute free consultation with Intuz AI experts to discuss your IoT-based predictive maintenance needs.