Table of Content
Here is a question for you: When was the last time you made an important decision about your manufacturing operations? Was it six months ago? A few weeks ago? A year ago?
OK. Now, did you trust your intuition when taking a call, or did you actually gather information to guide your action? We are guessing it was the latter. We hope it was the latter!
When one thinks of manufacturing, it is easy to picture a series of machinery doing their job and human personnel overlooking everything. However, data forms the core of manufacturing. It defines the processes and transforms businesses. Yes, that is right!
The statement is true across industry niches and is also true in CNC manufacturing, job shops, and other machine-intensive operations where data influences the workflows. Data is the key to maximizing profitability - even at factories and manufacturing plants in this day and age.
Digital technologies have enabled us to convert our routine machine processes into granular data - available at our fingertips. We can enjoy real-time visibility into our machine performance and make more targeted improvements with “machine monitoring.”
But what does the term mean? Is it exactly what it says? In this article, we will discuss everything there is to know about machine monitoring, starting with its definition:
What do you mean by machine monitoring?
As the name suggests, machine monitoring refers to the process of storing and displaying data extracted from machines in an industrial context.
It is a fast and highly scalable technique that helps you keep track of the machine’s performance, resource analysis, and production efficiency. Machine monitoring helps observe machine-based processes in a stable operating environment.
A brief history of machine monitoring
The modern manufacturing shop floor makes use of various types of equipment. The diversity makes it difficult for shop managers to monitor every piece of equipment with equal expertise and concentration.
Ever since the industrial revolution began, machines have been monitored by manually collecting data. But that was not a problem since the machines were relatively simple, with no sophisticated controls.
The information gathered was satisfactory and could be easily used for making simple decisions on how to sustain the status quo of machine operation and maintenance.
However, as new technologies emerged in the field of machine controls, the need to incorporate advanced machine monitoring systems gained traction in the manufacturing industry.
Research shows that half of the manufacturers already have some experience with condition-based maintenance, which means they are using some form of machine monitoring system, thereby establishing greater production efficiency.
Ready to Revolutionize Your Machine Monitoring With Advanced Industrial IoT Solutions?
Talk to ExpertsHow machine monitoring works
The main industrial goal of machine monitoring is to maximize profits, enhance productivity levels of those working on the shop floors, and minimize costs - without compromising the product or service quality. Here is how the concept of machine monitoring unfolds:
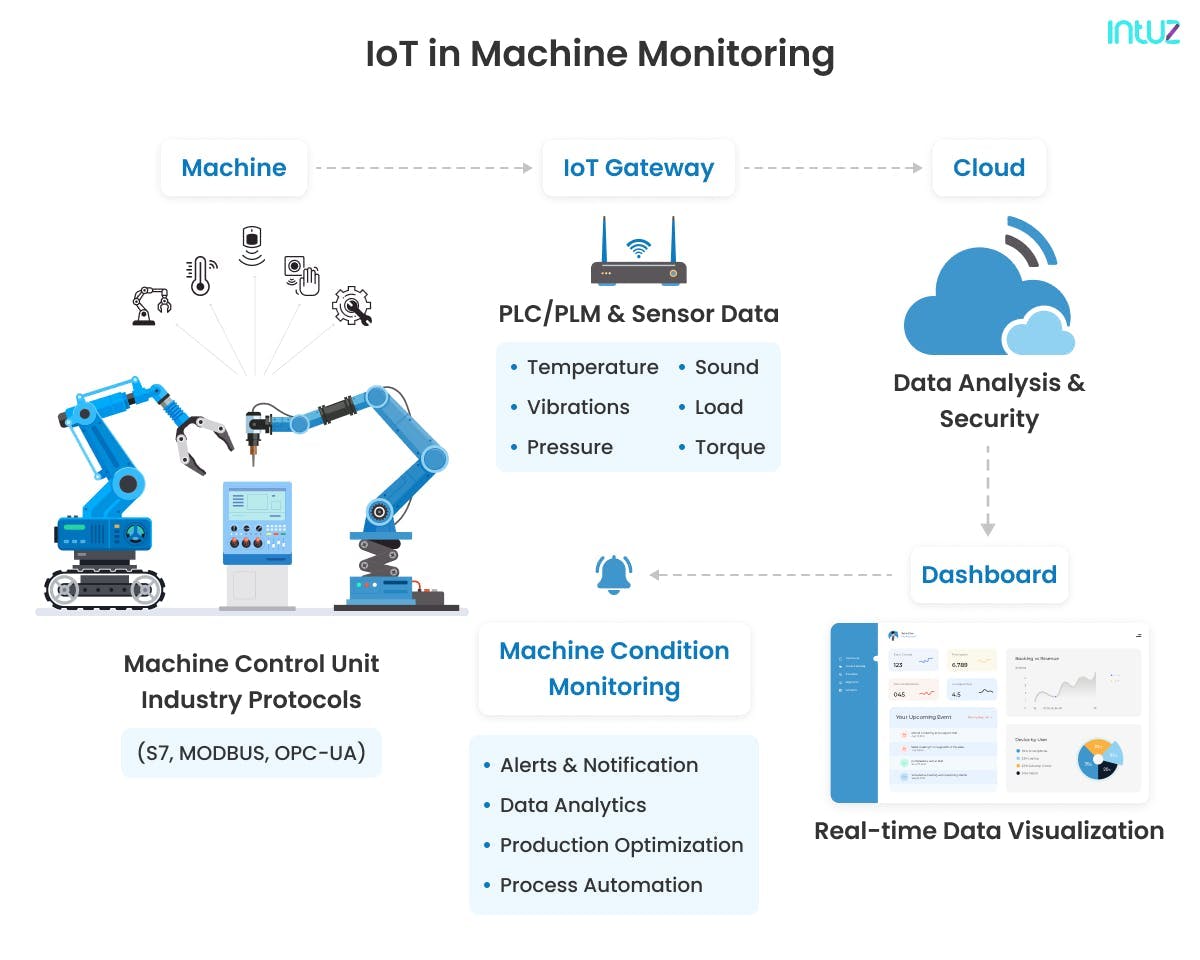
How IoT in Machine Monitoring Works
- Collect data from every machine and its operator on the shop floor. Having touchscreen tablets allows additional human context to machine data.
- Secure the data through an onsite IoT gateway, protecting your machine network from the public internet. The data is encrypted and stored in the cloud.
- Access to the data is given to the concerned authorities, who can securely use it on the shop floor, desktop, or mobile dashboards.
- Visualize data using real-time dashboards on the shop floor, indicating if jobs are performing at or below expectations.
- Monitor machine conditions - faults, work-order status, tool utilization, quality tracking, and downtime.
- Analyze using robust and superior reporting features. Get reports on the job status, downtime timelines, quality assurance, and so on, and compare the data by shift, machine, and individual job or parts.
Take corrective measures to rectify production bottlenecks, improve operational efficiency, and enable the digital transformation of your shop floor.
Advantages of machine monitoring
Manufacturers that leverage machine monitoring increase production by making quick and precise decisions driven by data, enabling real-time communication between the shop floor, operators, and management. Here are the top six benefits of machine monitoring:
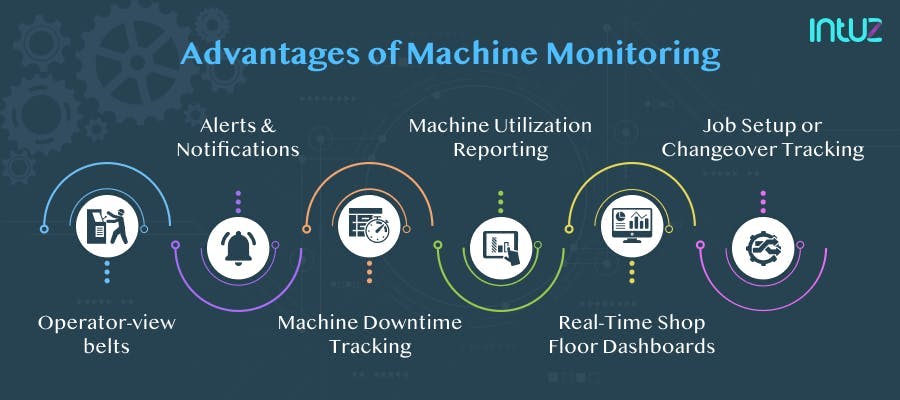
Advantages of Machine Monitoring
1. Operator-view belts
A touchscreen interface - mounted right at the machine tool - allows operators to add human context to machine data. You can think of it as a “Google Maps for operators” as the “Operator View” will enable them to categorize downtime, reject a part, and start or stop jobs right from the machine to manage and record quality data.
2. Alerts and notifications
When a machine malfunctions or is about to go down, a text alert can be sent to the managers not on the shop floor so that they can take prompt action. These alerts are customizable, allowing them to notify the right person at the right time when an issue arises.
3. Machine downtime tracking
Knowing why machines are not running, as usual, is key to understanding and reducing machine downtime and utilization problems. Therefore, having a touchscreen on each machine with an intuitive interface asking the operator to categorize downtime in real-time helps.
Managers can quickly review Overall Equipment Effectiveness (OEE), identify issues related to specific machinery, and measure the effect of process improvements.
4. Machine utilization reporting
Manage and view the real-time status of your machines across multiple departments and geographies with ease. Monitor machine utilization over a period of time and compare your manufacturing unit’s data against industry benchmarks. Evaluate utilization trends over time and justify the purchase of new machines by calculating excess capacity.
5. Real-time shop floor dashboards
Such dashboards give factory workers the information they need to make decisions for improving processes.
A simple color-coding technique indicates whether the machine performs at par or below the expectations - in real-time. These dashboards are installed on monitors across the shop floor at each cell and can be accessed by operators managing the floor.
6. Job setup or changeover tracking
Shop floors tend to change jobs frequently. This can be a significant source of lost production time for a business. Setup times for the same job differ from operator to operator. Machine monitoring systems help track setup time when dispatching jobs.
Once the job enters the setup, the “Operator View” calculates the estimated setup time. This data is available for reporting and can be exported as a CSV file for further analysis.
Machine monitoring and IoT: A match made in heaven
Before industrial IoT monitoring systems came into play, machine workers would manually investigate machine status - risky and time-consuming. This also often resulted in a higher risk of unplanned downtime and higher costs to resolve those issues.
Every machine was considered a standalone entity, meaning it was difficult for operators to fix the machines that were hampering production. Moreover, the data gathered was disjointed and, of course, not up-to-date.
Naturally, things radically improved when IoT technology entered the scene. For one, IoT promotes interconnectedness among machines and utilizes sensors to collect machine information.
These devices can be embedded in the machinery and assembly lines in a factory and convert data into analytical information useful for the managers. IoT-powered sensors initiative a human-to-machine interaction and carry forward more productive labor.
Applications of machine monitoring IoT solutions
IoT integration makes manufacturing more efficient through advanced sensor devices, a user-friendly dashboard, and robust gateway connectivity. Knowing the historical patterns and real-time performance of machine operations is possible thanks to IoT. Come, let us take a look at what magic you can weave in machine monitoring through IoT:
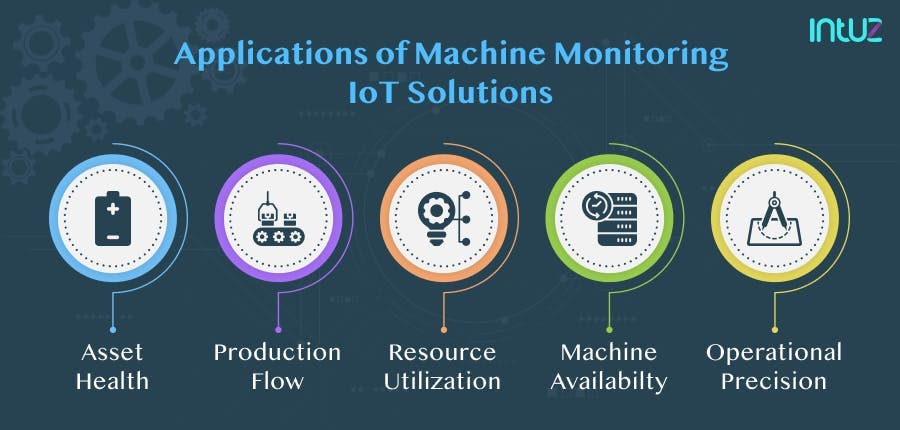
Applications of machine monitoring IoT solutions
1. Asset health
The whole point of using advanced technologies in your manufacturing unit is to keep an eye on how well your machines perform. Therefore, determine the health and performance of the equipment by tracking various parameters such as pressure, noise, temperature, and vibrations.
2. Production flow
If you want to know the exact position of a product on the shop floor - whether it is on the assembly lines or conveyor belts - IoT solutions can make that happen. Track each movement of the manufactured product for quick shipment and delivery.
3. Resource utilization
Calculate the consumption of resources such as electricity, fuel, lubricant, coolant, and so on with the help of IoT. Enhance the efficiency of your machines and reduce excessive wastage.
4. Machine availability
You can monitor the time when the machines are not running as they do, calculate the equipment downtime, and find the source of the shutdown through IoT-connected devices. Make things simple!
5. Operational precision
You can program machines through codes for precisive machine operability if you have machines running on digitized numerical controls. Enable efficient program optimization by studying tool lifecycle and feed rate. This helps in increasing machine accuracy.
Types of conditions to monitor in a machine
An unlimited number of conditions can be monitored on a machine because of the wealth of data you have in your hands. However, this can be time-consuming, if not expensive, so you need to identify conditions that will help you maintain the equipment properly. Fret not - we have done our homework.
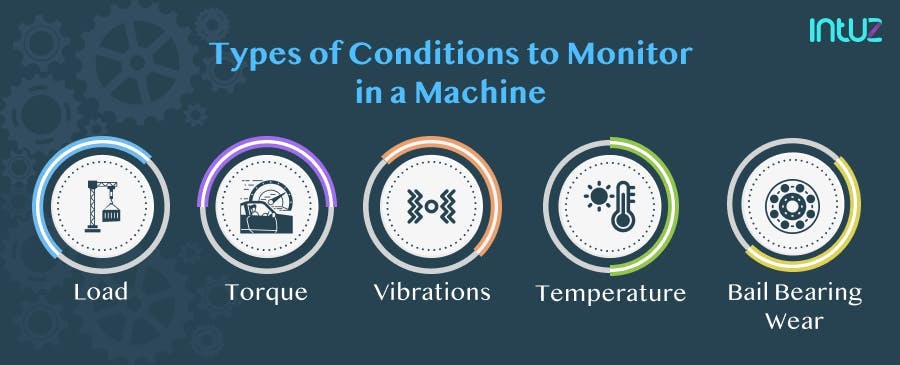
Types of conditions to monitor in a machine
In addition, you can add external sensors or connect older equipment with analog and digital IO to ensure everything gets monitored. Here are the top five conditions you can track to identify trends, predict failures, and execute timely maintenance:
1. Load
When a machine works on material over time, it becomes naturally dull, forcing the former to increase the load to ensure a proper cut. This is similar to how you may apply more pressure to an unsharpened pencil when writing. When the load increases, operators get notified and can make appropriate changes to the machine.
2. Torque
Are you looking to identify anomalies in the rotational force of the machine? You must better understand how the machine performs during job runs and find any correlation between machine failures, scrap parts, and broken tools.
3. Vibrations
Studying vibrations offers insight into how well or poorly a piece of equipment performs 15 minutes before the problem becomes visible to the human operator.
4. Temperature
This is an apparent indicator of potential problems in a machine. Monitoring equipment temperature or health risks can alert those on the shop floor of any looming machine failure or mishaps (downtime or fire) - especially in hostile manufacturing environments.
5. Ball bearing wear
This type of wear can damage the manufacturing equipment. It usually happens during startup or downtime when the fluid pressure in the machine is not high enough, causing much friction. By monitoring the condition of bearings, costly maintenance costs and downtime can be minimized drastically.
A Guide On The IoT Solutions For Smart Elevator Management
Learn MoreThree questions to ask before choosing a machine monitoring platform (or building one!)
Suppose you have decided to take the plunge and monitor your machines correctly; that is good for you! But equipment monitoring is only as good as the technology used. Therefore, here is a list of questions you should ask potential vendors before making a decision:
1. How easy is the tool for operators to use?
First, you do not want to get a solution onboard that your team cannot use. Whatever you choose - make sure it empowers engineers, operators, and management. If it requires a little training, ask your vendor to be clear about that beforehand so that you can make arrangements accordingly.
2. How easy is it to access machine data on the platform?
Are you looking for solutions that make it easy for you to store and access custom tables without writing a single query? Machine monitoring aims to increase data quantity and quality for more positive improvements.
That is why there is so much emphasis on making the data accessible to all stakeholders. Enable your manufacturing engineers and managers to work directly with data.
3. Is it possible to build custom states and track custom parameters?
Every shop floor is unique and has different demands. Not every vendor you speak to will have experience building solutions that cater to needs similar to yours. Therefore, ensure your software empowers you to add custom columns and tables, creating a picture of machine performance.
The Evolution Of Industrial IoT Monitoring Solutions In 2023
Read NowOver to you
Without machinery, no industry will be able to grow. Therefore, deploying an IoT-powered machine monitoring software solution makes a lot of business sense to ensure the machines do their job and are maintained at all times.
As discussed previously, many domains have already started implementing connected technology to bolster their productivity and efficiency.
Machine monitoring is the first step toward Industrial IoT (IIoT) because of its potential to build next-level communication networks using predictive maintenance, data representation, automation, and support.
Book a 45-minute free consultation with our IoT experts today and get a complimentary strategic roadmap for monitoring machines with advanced IoT technologies.