Table of Content
Corrosion in industrial piping refers to the gradual degradation or destruction of metal pipes, tubes, or vessels due to electrochemical or chemical reactions with the environment or process fluid. This can weaken the pipe’s metal, cause leaks, or even lead to disastrous failures if not properly detected and prevented.
Let us take a look at how corrosion is a significant problem in many industries and how IoT can help prevent production downtime, safety hazards, and increased maintenance costs:
Industries using industrial pipes that have corrosion problems
The issue of corrosion is a crucial problem with global implications, affecting both natural and industrial environments. It is now widely recognized that corrosion and pollution are closely linked, with many pollutants exacerbating the corrosion monitoring system.
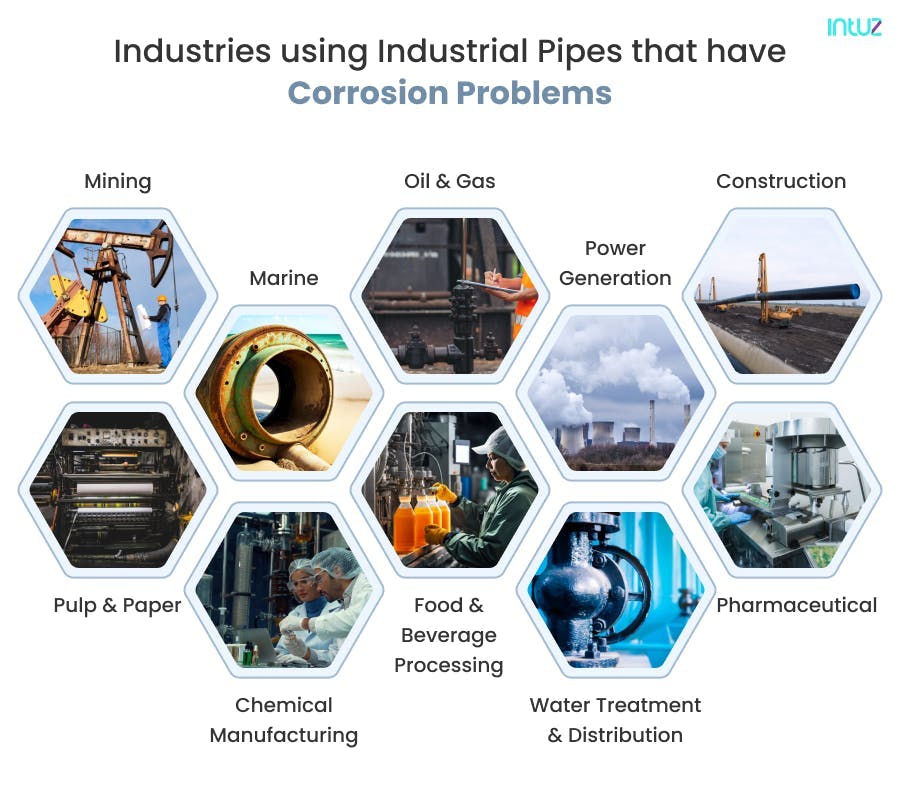
Several corrosion elements, such as rust, also contribute to the pollution of water bodies, which negatively affects the effectiveness of industry and the longevity of infrastructure assets. Here are ten industries using industrial pipes that deal with corrosion:
1. Mining
Mining relies heavily on metal piping systems to transport various materials throughout the mining process, including water, slurry, and chemicals. The corrosive environments in which these pipes operate cause significant corrosion problems, including internal and external corrosion, erosion, and stress corrosion cracking.
2. Marine
The industry faces corrosion problems due to increased exposure to saltwater and despotic environmental conditions. Corrosion can occur in the hull, piping, and other metal structures of ships, offshore platforms, and other marine infrastructure.
3. Oil and gas
The industry deals with corrosion due to the nature of its operations, which involves transporting and storing corrosive fluids and gasses over long distances.
The pipelines, tanks, and other equipment used here are exposed to harsh environments, including high temperatures, increased pressures, and corrosive substances like hydrogen sulfide and carbon dioxide.
These conditions can cause corrosion, resulting in pipeline leaks, equipment failures, and other safety hazards. For example, in 2010, the Deepwater Horizon oil spill in the Gulf of Mexico was caused by a failed corroded pipeline.
Let's Integrate IoT to Solve Corrosion Issues in Your Piping Systems!
Contact Us4. Construction
The industry faces corrosion problems in infrastructure such as bridges, tunnels, and buildings. Corrosion can occur due to exposure to weather conditions, humidity, and chemical substances. It affects the structural integrity of buildings and other structures, leading to costly repairs and potential safety hazards.
5. Pulp and paper
The industry uses various acidic and alkaline chemicals in their production process that can lead to corrosion in the pipelines and other equipment. For example, chlorine dioxide in bleaching causes severe corrosion in pipelines and valves.
Besides, moisture in the production environment can accelerate corrosion rates, leading to frequent maintenance and equipment replacement.
6. Pharmaceutical
Pharma companies use various materials and substances to manufacture drugs and medications, which can cause corrosion in the pipes and other equipment used during manufacturing.
Additionally, the pharmaceutical industry must maintain strict cleanliness and hygiene standards, using raspy cleaning agents causing corrosion. This contaminates the drugs and medications being produced, posing severe health risks to consumers.
7. Power generation
The industry, which includes power plants and transmission lines, is susceptible to corrosion due to exposure to high temperatures, humidity, and chemical substances. Corrosion can affect pipes, boilers, turbines, and other equipment, reducing efficiency and increasing maintenance costs and potential safety hazards.
8. Chemical manufacturing
The industry faces corrosion problems due to using corrosive chemicals in various manufacturing processes. Corrosion can occur in pipelines, storage tanks, and other equipment transporting, storing, and processing chemicals.
This can lead to leaks, product contamination, and equipment failure, resulting in safety hazards, production delays, and significant financial losses.
9. Food and beverage processing
The industry uses various types of pipes, such as stainless steel and plastic, to transport different products and liquids throughout manufacturing. These pipes are subject to corrosion from their materials, including acids, sugars, and other chemicals.
In addition, the cleaning agents used in food and beverage processing facilities can be corrosive and contaminate the products and liquids, causing equipment failure and production downtime.
10. Water treatment and distribution
Corrosion in this industry can result in water quality issues, leaks, and the breakdown of infrastructure, leading to costly repairs and service disruptions. For example, in 2015, Flint, Michigan, faced a water crisis due to corroded pipes that allowed lead and other contaminants to leach into the drinking water.
How IoT sensors detect and prevent different types of corrosion in industrial piping
The term “Internet of Things” (IoT) describes a system of physical objects, including vehicles, appliances, and devices, that are equipped with sensors, software, and internet connectivity to exchange data.
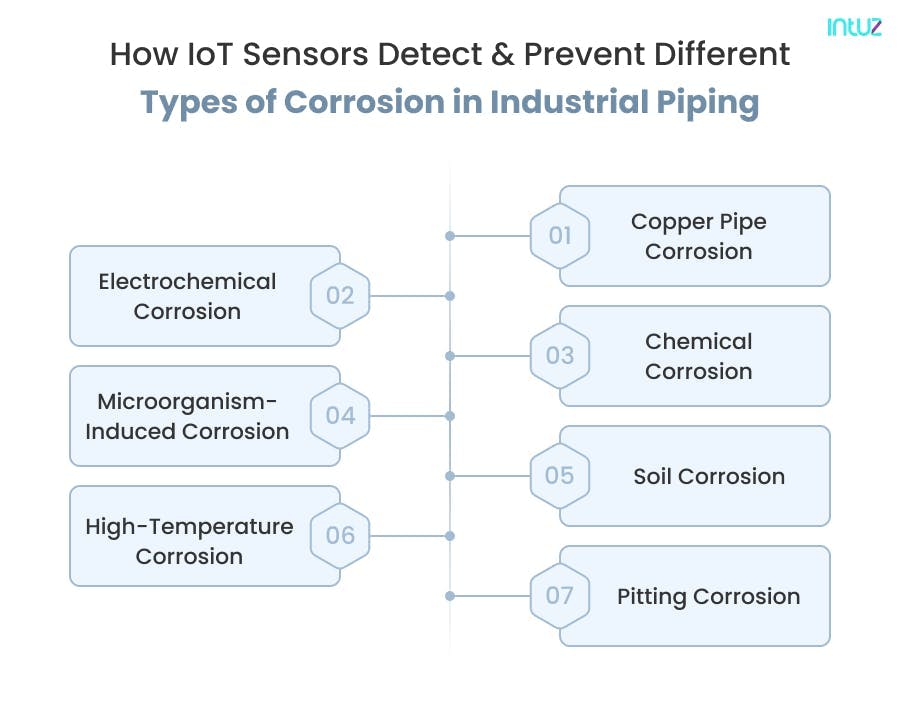
IoT-driven corrosion monitoring in piping systems enhances worker productivity, safety, and equipment efficiency through the analysis of data collected by these devices. By continuously monitoring the conditions inside and outside pipes, IoT sensors detect the changes that may lead to corrosion and take preventive measures before it is too late.
Here is a closer look at seven significant types of corrosions in industrial piping and how IoT for corrosion monitoring works its magic:
1. Soil corrosion
Buried pipelines and structures can experience soil corrosion, which is influenced by the chemical and physical properties of the surrounding soil. IoT helps reduce soil corrosion by monitoring soil parameters such as moisture, pH, and temperature.
The sensors prevent excessive moisture buildup around underground pipelines and structures, accelerating soil corrosion. The technology also monitors the chemical composition of soil and alerts operators if the soil is becoming too acidic or alkaline, thereby enabling informed decisions about preventive maintenance and avoiding costly repairs.
2. Pitting corrosion
This is a localized form of corrosion that forms small holes or pits in the metal surface. It occurs when there is an uneven distribution of oxygen or other corrosive substances across the metal surface. IoT sensors can monitor the temperature and humidity of the environment and detect the presence of corrosive substances such as chloride ions, monitor the integrity of the metal surface, and detect any changes in the oxide layer that could lead to pitting corrosion.
3. Chemical corrosion
It can be caused by exposure to acidic or alkaline substances, such as those commonly found in industrial processes. Oxidation reactions, where metal surfaces react with oxygen, can also cause chemical corrosion.
IoT sensors can automate the addition of corrosion inhibitors into the system, which are chemicals added to the environment to prevent the corrosion of metal surfaces. The technology also monitors the condition of the metal surfaces, such as the thickness of the protective coating, and alerts operators if there is any degradation.
IoT Operational Technology (OT): Convergence With IT & Key Differences
Learn More4. Copper pipe corrosion
Copper pipes are susceptible to corrosion caused by chemical reactions between the water and the metal, which can result in pinhole leaks and other types of damage. By monitoring water quality parameters such as pH, alkalinity, and dissolved oxygen, IoT sensors detect when the water chemistry is becoming corrosive and alert operators to take corrective action.
IoT can also help prevent copper pipe corrosion by controlling the water flow rate and temperature. High water flow rates and temperatures can accelerate corrosion, so IoT devices can regulate these parameters to prevent excessive wear on the pipes.
5. Electrochemical corrosion
This type of corrosion occurs when two different metals are in contact with an electrolyte, such as saltwater or acidic fluids. This creates a flow of electrical current between the metals, causing the more active metal to lose electrons and corrode.
Electrochemical corrosion can be prevented by using compatible metals or isolating them from the electrolyte. IoT sensors, for instance, can detect changes in the electrolyte and adjust conditions by adding inhibitors or changing the metal to a more compatible one.
6. High-temperature corrosion
This occurs in high-temperature environments, such as in power plants or industrial furnaces. The rapid metal degradation in these environments occurs due to reactive gasses or other substances.
IoT can prevent high-temperature corrosion by monitoring the temperature and humidity of the environment where the equipment is operating. By keeping track of these factors, IoT sensors adjust the conditions to minimize the likelihood of corrosion.
IoT monitors the chemical composition of the fuel being used and adjusts the combustion process to reduce the formation of corrosive byproducts. It alerts operators if there are any signs of corrosion or wear, allowing for timely maintenance and repair to prevent further damage.
7. Microorganism-Induced Corrosion (MIC)
MIC is a type of corrosion that occurs when certain microorganisms, such as bacteria or fungi, directly attack the metal inside pipes by consuming the material. This can cause pitting or general corrosion, which weakens the pipe’s structural integrity and leads to leaks or failures.
MIC affects the internal and external surfaces of pipes and structures, which poses a significant problem in pipelines carrying water, oil, gas, or other fluids.
IoT sensors monitor the condition of pipes and structures, such as for changes in pH levels, oxygen levels, and corrosive substances like sulfides or acids. Corrosion detection and prediction using IoT and Machine Learning help schedule maintenance or repairs before the corrosion causes damage.
Benefits of using IoT sensors for corrosion prevention
IoT sensors can provide real-time data on the corrosion rate, enabling maintenance teams to take immediate action if the corrosion rate increases. IoT also ensures the following:
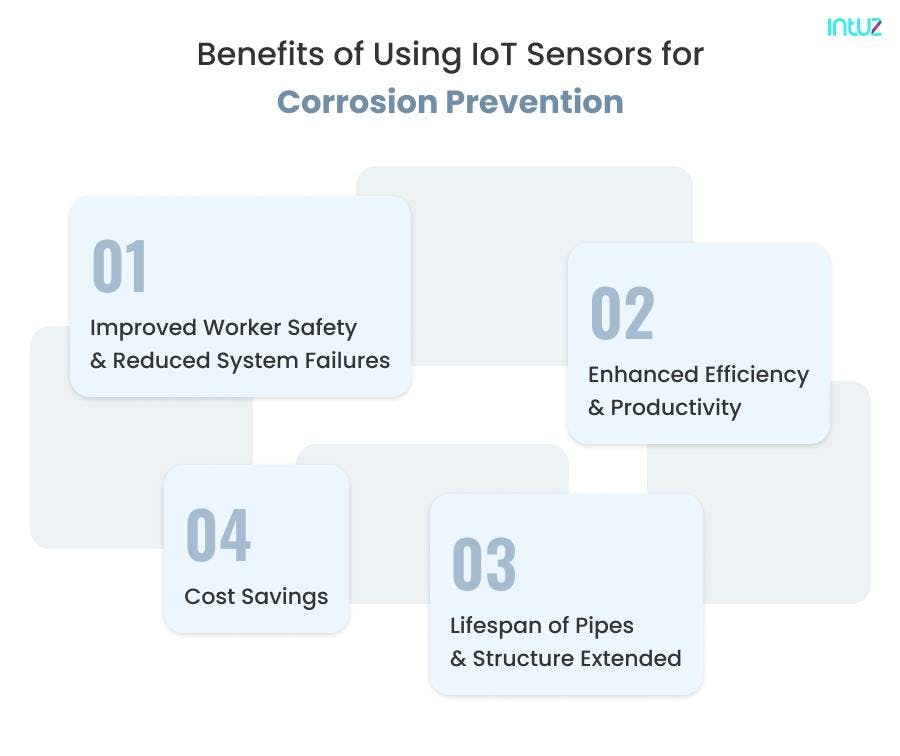
1. Cost savings
IoT sensors can monitor equipment and predict when maintenance is required, reducing unplanned downtime and associated costs. Sensors also detect inefficiencies in equipment, allowing for adjustments to be made to reduce energy consumption and costs.
2. Enhanced efficiency and productivity
IoT sensors can collect vast amounts of data from various sources in real time. This enables more efficient decision-making, as the data can be analyzed and acted upon quickly. For example, sensors can optimize the flow of oil or gas through pipelines, thereby reducing wastage and increasing productivity.
Quality Control In The Age Of IoT Development Services: A Quick Glance
Learn More3. Lifespan of pipes and structures extended
With continuous IoT monitoring and data analysis, operators can identify corrosion and other issues early before they lead to massive failures or leaks.
This enables scheduled proactive maintenance and repair work, which can extend the lifespan of pipes and structures. For example, operators may apply protective coatings or install sacrificial anodes to slow down the rate of corrosion.
4. Improved worker safety and reduced system failures
IoT sensors can improve safety by reducing the need for workers to inspect pipelines and structures in hazardous environments physically. By transmitting data wirelessly, workers can monitor conditions remotely from safe locations, thus minimizing the risk of accidents or injuries in the workplace.
Protect Your Industrial Piping: Contact Us for IoT-Powered Corrosion Control!
Contact UsOver to you
IoT has revolutionized corrosion inspection and monitoring for many industries, providing a universal solution to worker safety, equipment performance, and cost savings.
Real-time IoT-powered corrosion monitoring provides data for timely preventive actions and predictive analysis.
Book a Free 45-minute Consultation with Our IoT Experts Today! Get a customized roadmap and strategies to leverage IoT to solve pipe corrosion issues.