Table Of Content
As enterprises across sectors continue to generate increasingly large volumes of data about the physical ecosystem, the need to map this data back to the IT platforms for better defining user behavior and product relevance along with enhancing the digital thread is even higher.
Connecting digitally and modeling physical products or assets is what enterprises want to focus on in the coming years. And that is where digital twins enter the picture — a type of technology which enables highly sophisticated analysis and advanced simulation.
The definition of “digital twin”
In simple words, a digital twin represents any physical object in a digital form. It is a replica of the original device. It is often used in the field of IT by data scientists and analysts who want to run simulations before actual devices are developed and deployed.
The digital twin technology had first found its use in the manufacturing sector but is now expanding in broader and diverse fields such as the Internet of Things (IoT). Besides, the concept has become helpful in data analytics and Artificial Intelligence technologies.
A Gartner research shows that 13% of organizations implementing IoT projects already utilize the digital twin technology, while 62% are either in the process of starting to use it or planning to do so. The digital twin market is predicted to grow to $35.8 billion by 2025.
The story behind the digital twin
The digital twin is based on the concept of creating a model of a large object or product that has to be manufactured on a large scale, beforehand in a smaller version so that any problems or issues that can be encountered later on will be detected earlier in this stage.
This way, manufacturers could reduce losses that might have been incurred if these errors were not identified and corrected on time. Today, even more important things like buildings, factories, and other facilities are being included, expanding the concept exponentially.
The technology was first created by NASA, where they built a mock-up version of real space capsules to check for any error that might occur when they were orbiting in real-life. Further, it is being said that people, cities, and processes can have digital twins in the future.
Cutting-edge Industrial IoT Solutions and Development Services Company!
Explore services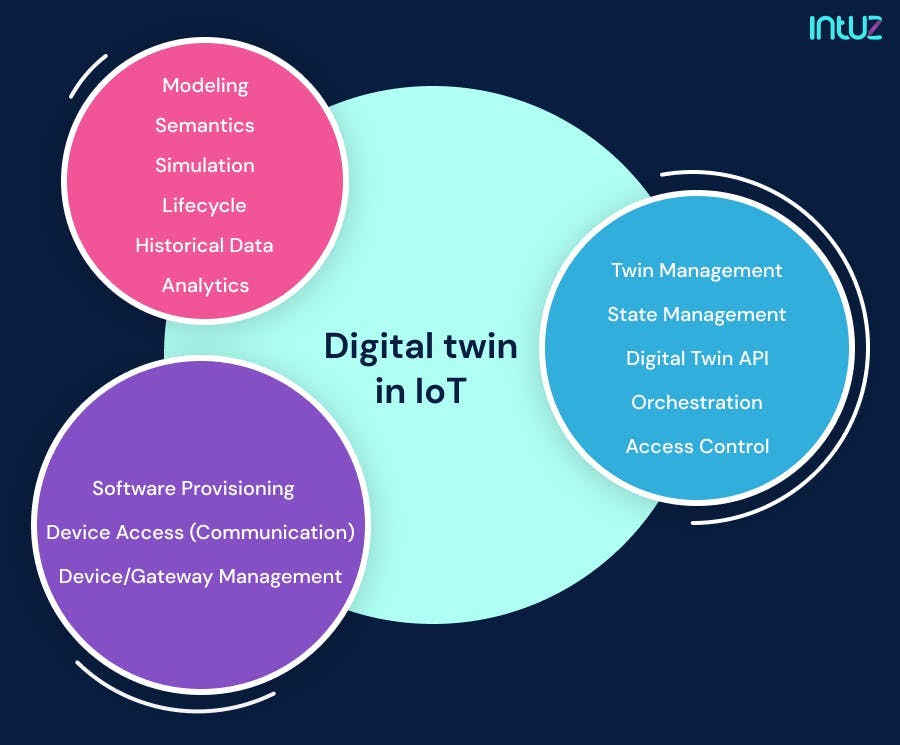
The importance of a digital twin in IoT
Before we look into the relationship between the two, let us first understand what IoT actually is. Short for the Internet of Things, it is similar to a digital network connecting many devices via the Internet. And it is something that is slowly paving its way in every aspect of human life.
In essence, IoT describes physical objects embedded with sensors, processing ability solutions, and other technologies that connect and exchange data with other systems and devices over the Internet or other communications networks.
Clearly, the rise of IoT sensors is partly responsible for making digital twins possible. As IoT devices are refined, digital twin scenarios can involve smaller and less complicated objects.
The technology digitally represents a physical machine, vehicle, or device on an IoT platform. This way, you can virtually access all of the processes, data, operational states, and life cycle of a specific physical asset.
Digital twins help IoT systems in the following ways:
1. Status of the device
In IoT, since the Internet interconnects all devices and machines, a digital twin helps determine how they are operating in real-time. This allows one to access information about their status much easier and quicker — a boon in sectors like patient healthcare.
2. Documentation and communication
Every machine has its own set of behaviors and processes that are unique to it. Creating a digital twin model helps understand these behaviors better and document that information appropriately. No more relying on physical records!
3. Predictive modeling
The digital twin technology helps analyze the future state of the machine or device. This allows the providers of IoT development services to create a functional IoT model that can predict whether the state of the concerned IoT machine would be in a better condition in a specific timeframe and whether it would adapt to the changing processes later.
4. Measurement of different outcomes
The digital twin model of a machine or device can be used to measure different possible outcomes for a process by changing the input variables. This way, digital twin models help one estimate data without losing time and money in IoT product development systems.
5. Risk reduction
IoT gives access to a large population of devices simultaneously. A minor security loophole can provide hackers with room to gain unauthorized access to the IoT network. This risk is magnified when the actual physical devices are deployed in production.
Digital twins eliminate that risk and allow developers to safely experiment with multiple scenarios before arriving at one, which is operationally feasible and secure.
6. Integration of systems
The supply chain consists of a large set of operations, starting from production, storage, transportation, and the shipment of goods. A variety of backend applications can be interconnected to receive accurate data about the supply chain operations in real-time.
7. Efficient experiments
Experiments of any kind are tedious and incur expensive resources. Since IoT is a relatively new technology, there is considerable scope for experimentation, which needs to be carried out with reasonable resource usage.
Digital twins offer the virtual infrastructure needed to conduct multiple experiments when not many physical devices are available.
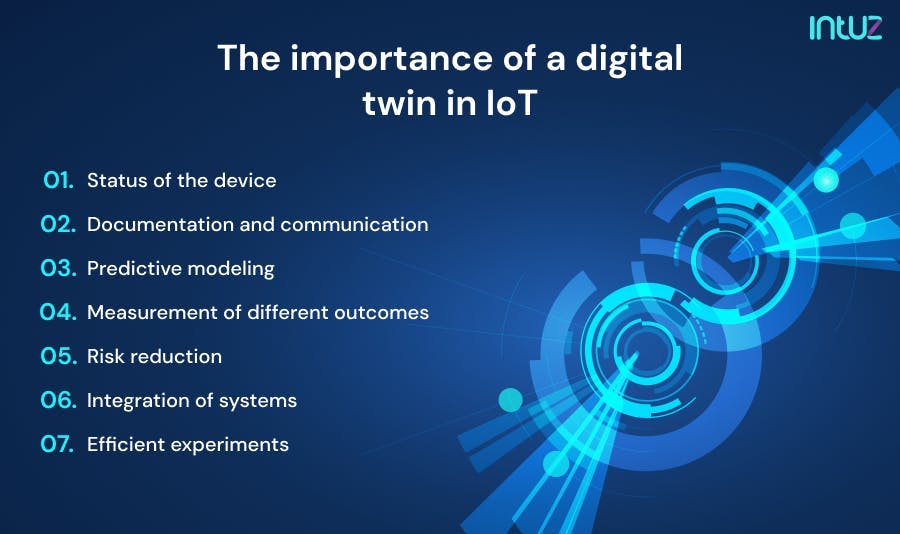
The types of digital twins
A product development life cycle consists of many stages. Different types of digital twin models can be employed based on where the development stands. It is common to have different types of digital twins co-exist within a process or system.
Overall, they can be categorized into product digital twins, production digital twins, and performance digital twins.
The three types provide data about the product from all the product life cycle stages. They are collectively known as a “thread.” Let us read on to find out more about each of these digital twins in greater detail:
1. Product digital twin
This digital twin model is used to produce a new product efficiently. It helps in digitizing a product to detect its performance level. It also helps in determining how the products are performing in real life.
No matter how complex a device or system is, the product digital twin can be used to analyze all the possible challenges in product development and effectively use IoT software solutions to eliminate any defects.
Why should you use a product digital twin?
It eliminates the need for many prototypes.
The total time required to develop a product is reduced.
It provides a faster way of implementing feedback from customers.
The final manufactured product is of better quality and delivers higher performance.
2. Production digital twin
As the name suggests, this digital twin model is used in the production line. The manufacturer can, for instance, validate how well a manufacturing process will work on the shop floor by testing its efficiency using the production digital twin.
The technology helps determine the most beneficial processes that need to be eliminated. This way, factories and manufacturing hubs can design their production process in a way that is effective and efficient even if there are various changes in the outside environment.
In addition to this, using the data from the product or digital production lines gives insights into data that can be utilized for preventing any costly downtime to equipment.
Why should you use a production digital twin?
The whole manufacturing operation becomes faster and more efficient.
It helps predict any challenges in manufacturing and prevent them.
It prevents the loss of money caused by defective manufacturing processes.
3. Performance digital twin
This digital twin model collects data on daily operations and performance of products and plants, analyzes that data, and creates efficient methodologies.
Businesses need actionable insight to make apt decisions. The performance digital twin sources an ocean of data from various systems, giving information on the actions that need to be taken.
It helps improve the overall efficiency of the production system.
It helps in creating new businesses based on the performance data.
It helps collect data on daily operations, analyze the data, and use it to make informed decisions.
How does a digital twin work?
The data is delivered to the digital twin, which acts as a virtual system or product after gathering it. With the aid of this virtual representation, the actual object can be monitored and analysed in real time. The digital twin continuously gathers and processes the incoming data, establishing a feedback loop that allows for the observation, management, and study of the behaviour of the physical entity.
The digital twin copies the physical object's present state and models the object's behaviour under various conditions. The digital twin can offer insights into the future functioning of the physical device by combining historical data and predictive algorithms. The ability to forecast the future allows for proactive decision-making, optimisation, and maintenance.
Obtaining knowledge and making wise decisions enables engineers, operators, and other stakeholders to engage with the virtual product or system. Users may monitor and analyse the virtual equivalent in real-time thanks to visual representations and simple interfaces.
Utilising knowledge from digital twin
There are several ways to make use of the knowledge gleaned through the examination of the digital twin. For instance, locating bottlenecks, inefficiencies, or prospective improvement areas, can aid in improving the performance of the actual production process. The digital twin can assist in decision-making for process optimisation and resource allocation by simulating various scenarios and assessing the impact on performance.
The digital twin also makes applying adjustments and changes easier, promoting ongoing progress. The physical product or system can be designed and developed using insights from the digital twin, allowing for iterative improvements. Engineers can improve the virtual product by analysing performance data and user comments, which can subsequently be converted into improvements in the real world.
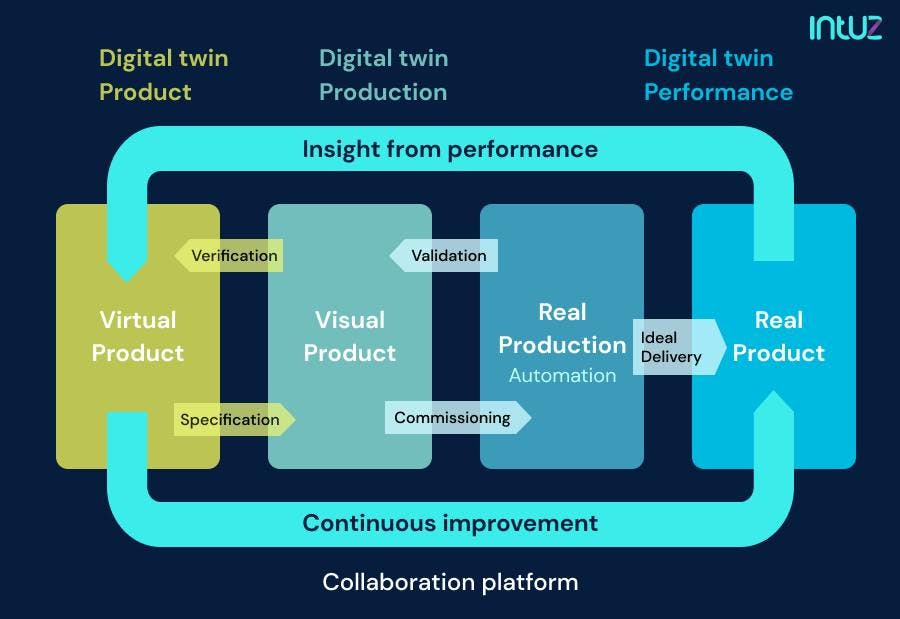
7 most practical applications of digital twins in IoT
Digital twins can be used in a wide range of fields. Vehicle manufacturers, for instance, build a digital twin of the car, plane, or ship they want to manufacture. They are then digitally tested for their performance and efficiency. But that is not it.
They act as a pillar of support for IoT projects in multiple industries. Digital twins are also used for other purposes such as the following:
1. Healthcare
Digital twins in healthcare bring forth innovations to monitor a patient’s condition. There are many different types of trackers that patients can wear, such as motion trackers, fitness trackers, wearables, and so on, to determine the heart rate, blood pressure, and other vitals.
The data is collected by digital twins and exchanged with the servers in real-time, thus eliminating the need to maintain physical records to help make better sense of the information so that the doctors can continually monitor a patient’s health without the patient being physically present for examination.
2. Utilities
Large machinery and equipment manufacturers also use digital twins. Artificial Intelligence technologies and IoT development services provide the necessary data to conduct tests and performance fixes.
Digital twins enable engineers to have “as-built” or “as-operated” versions of the utilities in a virtual environment. This reduces the possibility of mishaps causing downtime.
In addition, digital twins can monitor real-time power consumption, power outage prediction, and asset management without having personnel on-site.
3. Smart cities
Digitalizing cities can help better manage resources and develop more efficient safety precautions. In the case of natural disasters or unfortunate events, data can be collected from IoT systems (motion sensors, more specifically) to predict the likelihood of them happening.
Digital twins can then be used to design systems to help prevent disasters or reduce their negative impacts.
4. Urban planning
Civil engineers and other professionals involved in urban planning can leverage the power of digital twins as they can display 3D and 4D spatial data in real time and deploy augmented reality systems into built environments.
5. Supply chain and logistics optimization
Do you want to track every step of your supply chain process in real time? Using the digital twin with IoT can help you monitor the entire supply chain process starting from the procurement of raw materials to delivering the finished product.
The digital twin collects the data from IoT sensors and provides real-time monitoring of your supply chain. It helps you identify anomalies and deploys that occur.
Logistics is one of the most critical elements that affect the pricing and productivity of the supply chain. Digital twins combined with IoT technology allow for better scheduling and execution for automated and seamless logistic management.
6. Automotive design and testing
Automotive experts can test the design of their vehicles in different weather conditions, without building costly prototypes by unleashing the power of digital twin and IoT together. It helps identify the weaknesses in the vehicle and improve the design in a way that can perform effectively in different environments.
7. Smart manufacturing
Leveraging the power of digital win and IoT, manufacturers can monitor the condition of manufacturing processes to get insights into the performance of the equipment. With the help of analytical insights into the collected data, manufacturing companies can check the customers’ choices in terms of product purchase and accordingly make the manufacturing decisions. It helps reduce manufacturing costs while improving product quality and streamlined manufacturing processes.
The top digital twin vendors to know about
Creating a digital twin is a rather complex process, and there is not a single concrete platform that is suitable for all. However, all is not gloomy in this field.
Many digital twin vendors design such models for different purposes. The following are some of the top digital twin vendors in the world as of today:
1. Microsoft
Microsoft has launched Azure Digital Twins as a Platform as a Service (PaaS) enables the development of twin graphs based on digital models of environments — for instance, farms, railways, buildings, energy networks, and so on. These models help gain insight to drive better products, reduce costs and optimize overall operations.
2. Bosch
Bosch’s digital twin technology comprises the virtual representation of physical assets along with the functionality and information required for offering a holistic view accessible by APIs.
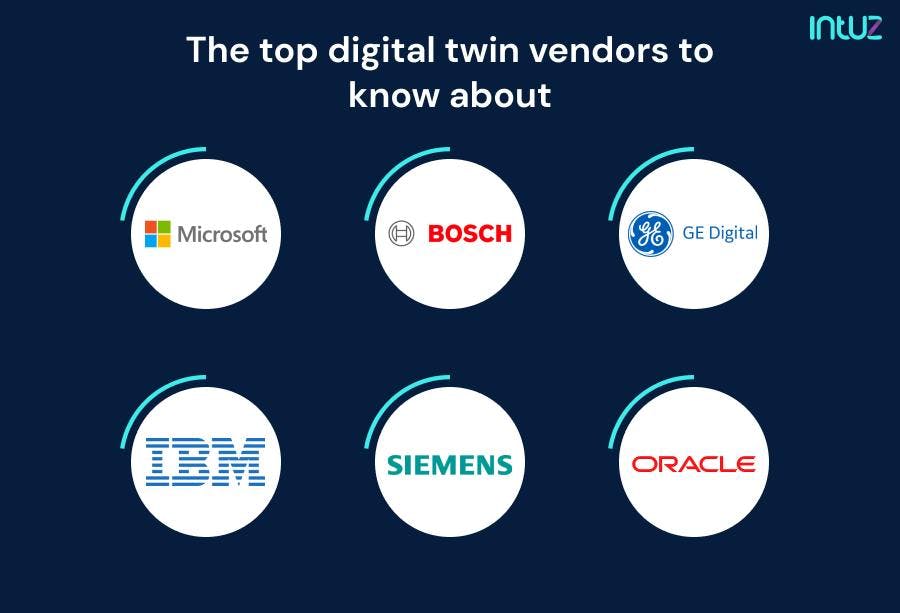
3. GE Digital
The company is focused on building the digital twin software so that it can help its customers in three core aspects — Network, Process, and Asset. For example, GE leverages digital twins in its jet engine manufacturing processes. The technology offers product quality insight into asset performance in real-time for influencing and customizing impact on the supply chain.
4. IBM
IBM is promoting the digital twin technology as a part of its IoT initiatives. The digital twins are constantly learning new skills and capabilities, which means they can keep generating the insights required for high-performing products.
5. Siemens
Another industrial giant involved in manufacturing, Siemens, is modifying the digital twin technology for its factory-floor suppliers. Using the data fetched from the technology, manufacturers can avoid costly downtime to equipment.
They can forecast when preventative maintenance will be necessary. This constant flow of information positively influences manufacturing operations and makes them more efficient, swift, and highly reliable.
6. Oracle Corporation
Their digital twin simulator lets you create simulated devices for your environment without installing or connecting to any software. Generate configurable alerts, live data, and events for such simulated devices. Control and monitor them in real-time. Configure them to generate events and signals. Add events, photos, and data sources to your simulators with ease.
Digital twins vs. Predictive twins
A digital twin is essentially a present-day model. In other words, it comprises all the data of a physical object and helps determine its performance, helping you with options that can be implemented in the present condition.
On the other hand, a predictive twin models the future behavior and state of the device, as the name suggests. It is based on historical data sets that have already been collected through IoT sensors. The information can help in simulating breakdowns that need attention, thus reducing company costs and downtime.
How to create a digital twin
Because it is such a new and unique technology, the process of creating a digital twin can be daunting. However, you have to start somewhere, right? And with proper guidance, you can. You can break down the development into three stages:
1. Design
Select the enabling technology you want to integrate within the physical asset to enable the real-time flow of data from IoT devices and the integration of transactional and operational information from other enterprises.
You must also determine the modeling software required for asset representation in 3D, the device type you need, or the person that needs to be given access to the information within the digital twin. The main aim of developing such a structure is to remove all risks.
Your digital twin must be able to authenticate, configure, monitor, and manage each device — virtually, of course. Besides, understand the type of information required to flow across an asset’s life cycle. After all, the goal is to store the data in such a way that is easily accessible.
2. Operation
Decide the function of your digital twin. What do you want it to do? Monitor the asset? Or control and modify the asset? Do you only want it to assist with predictive maintenance? The answer to these questions will determine the device types attached to the asset and whether you should employ more sophisticated devices for information processing.
Controlling how data sets are stored, prepared, and presented is vital for enabling advanced analytics. To achieve quality results, you must guarantee extremely succinct and polished data transmitting from IoT devices. Leverage an identity-by-design approach in such a case.
3. Development
Most digital twin deployments start small — for instance, monitoring the performance of a single element of an asset but expanding over time. Ideally, you could start by putting together smaller digital twins to get a complete picture of how the machine will operate.
If you want to modify any part of the digital twin, you will not have to rip it apart. Only replacing the layered functionalities within the digital twin to meet the evolving requirements will help.
Expert IoT App Development Awaits - Share Your Project Details!
Let's Get StartedOver to you
At the heart of every digital transformation initiative is a combination of edge-based and cloud technologies, including IoT, high-performing computing solutions, and advanced analytics.
These technologies are extremely helpful in designing efficiently-performing systems and machines. When used in developing systems with a hint of IoT, a digital twin becomes the asset a company needs. Here is a recap of some of the benefits of using a digital twin:
It helps form better manufacturing processes.
Any future changes and their outcomes can be predicted using it.
It helps build products and shorten the product development cycle.
It reduces costs by helping build a physical object first to detect errors.
It helps monitor real-time data and make effective changes based on performance.
Book a Free 45-minute Consultation with Our IoT Experts Today! If you are looking to get an IoT app developed and want a supplier that understands the technology properly.
From large-scale enterprises to startups, we specialize in developing intuitive digital experiences by leveraging technology.