Table Of Content
The modern industrial landscape is a hub of cutting-edge technologies. One of those technologies that is turning the tables is the Internet of Things. IoT is exponentially growing and penetrating the industrial landscape with its diverse applications and benefits.
It helps businesses improve productivity, safeguard workers’ health, reduce business costs, etc. However, the scope does not end here. With advanced IoT devices, businesses can safeguard their industrial machines.
Vibrations have critical significance among several machine health parameters, like temperature, pressure, etc. Therefore, they need close analysis to pinpoint the exact issue. In this blog, we will uncover the meaning of vibration diagnostics, the factors responsible for vibrations in a machine, and potential solutions to deal with them.
What is equipment vibration, and what does it include?
Equipment vibration refers to the oscillations and the abnormal back-and-forth movement exhibited by the machine during the operation. Some vibrations are normal; however, only a professional can judge them well.
These vibrations are silent messengers that convey the health and performance of the machine. Ideally, equipment vibration can be due to several factors, such as the working conditions of the machine, the type of machine, and its function.
For example, a manual metal-cutting lathe produces more vibrations than a CNC machine. Another example is oscillating sanders and vibratory tumblers. These devices use vibrations for operations. Hence, their vibrations are normal.
Now, if we talk more about the vibrations, they can be of several types based on frequency, aptitude, and phase. Therefore, a professional will be required to judge them.
Common Causes of Equipment Vibration
Before we discuss the challenges of traditional vibration analysis methods, let's take a quick look at those methods
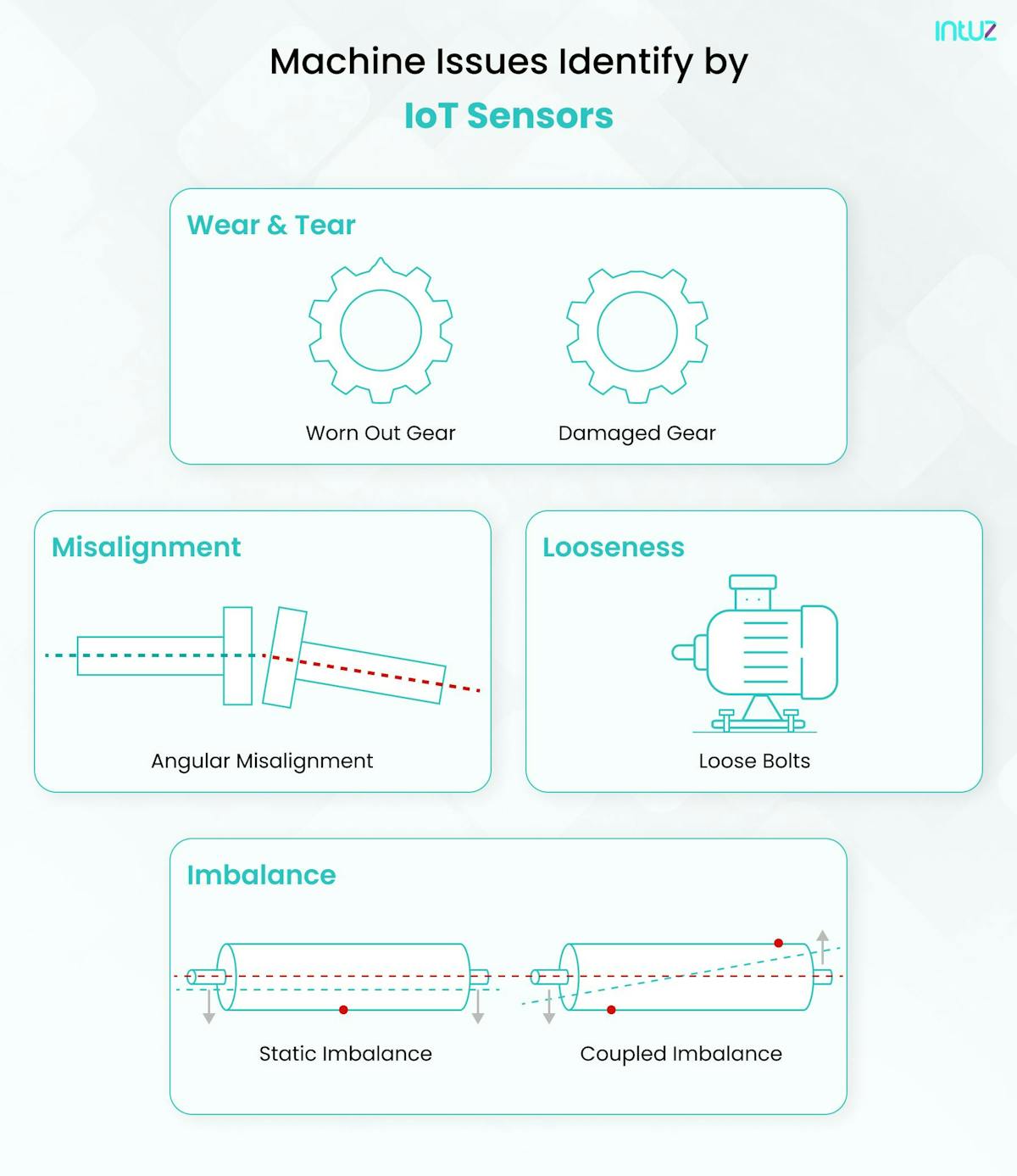
- Wear and tear: Wear and tear is one of the primary causes of equipment vibration. For example, a pitted roller bearing will cause vibrations when running on a damaged surface. Another example can be a chipped gear tooth, which may cause vibration when fitting into the other tooth. Regular visual inspections can help in the faster detection of wear and tear.
- Looseness: Most of the time, the machine has no technical faults or wear and tear. The vibrations are caused by the part that's not being bolted properly. Loose bolts can cause machines to vibrate. For example, in a vehicle, a loose bolt can cause the wheels to wobble. Regular visual inspection is the way to identify it.
- Imbalance: Imbalance is another common cause of machine vibration. An example of this can be missing balancing weights or deformed fan blades. Uneven weight in a machine rotating at the highest speed can cause catastrophic damage other than vibration. Vibration analysis methods like order analysis are useful in detecting imbalances as vibrations increase in a specific direction of rotation.
- Misalignment: Vibrations due to misalignment can be radial or axial. It is primarily due to the misalignment of the motor and pump axes. To identify misalignment, laser alignment tools like laser displacement sensors are used.
Do You Want to Reduce Downtime by Implementing IoT-Driven Vibration Monitoring?
Let's ConnectChallenges of Traditional Vibration Analysis Methods
As there is no use of sophisticated and advanced technology in vibration analysis methods, it introduces several challenges in the process.
Missed early warnings:
In the early stages, the vibrations from the equipment may be less intense and go undetected by individuals or traditional sensors. Therefore, the lack of proper sensors and human expertise may lead to missed early warnings. Consequently, this leads to catastrophic machine failure.
Absence of real-time data:
None of the traditional methods provided real-time or continuous data access. Thereby increasing the chances of missing vibration data in between the testing intervals.
Costly downtime:
Industries' greatest challenge with traditional vibration analysis or other condition monitoring methods is costly downtime. Using inaccurate vibration data and missed early warnings, industrial machines tend to break down more frequently. As per statistics, 42% of the unplanned downtown cost is due to equipment failure.
These are the primary challenges with traditional equipment vibration diagnostic methods. Besides these, the absence of advanced tools and techniques for in-depth analysis also poses a challenge for identifying specific faults.
The Use of IoT-based Vibration Diagnostics and its Benefits!
Thanks to its surging market, industrial IoT solutions are widespread across all industrial sectors. Whether it is manufacturing, telecom, aviation, or any other sector, smart IoT solutions detect machine issues in advance and plan predictive maintenance procedures.
Regarding vibration diagnostics, several IoT sensors are used for detecting a machine's vibrations. Here are some of the advanced IoT sensors used for vibration detection.
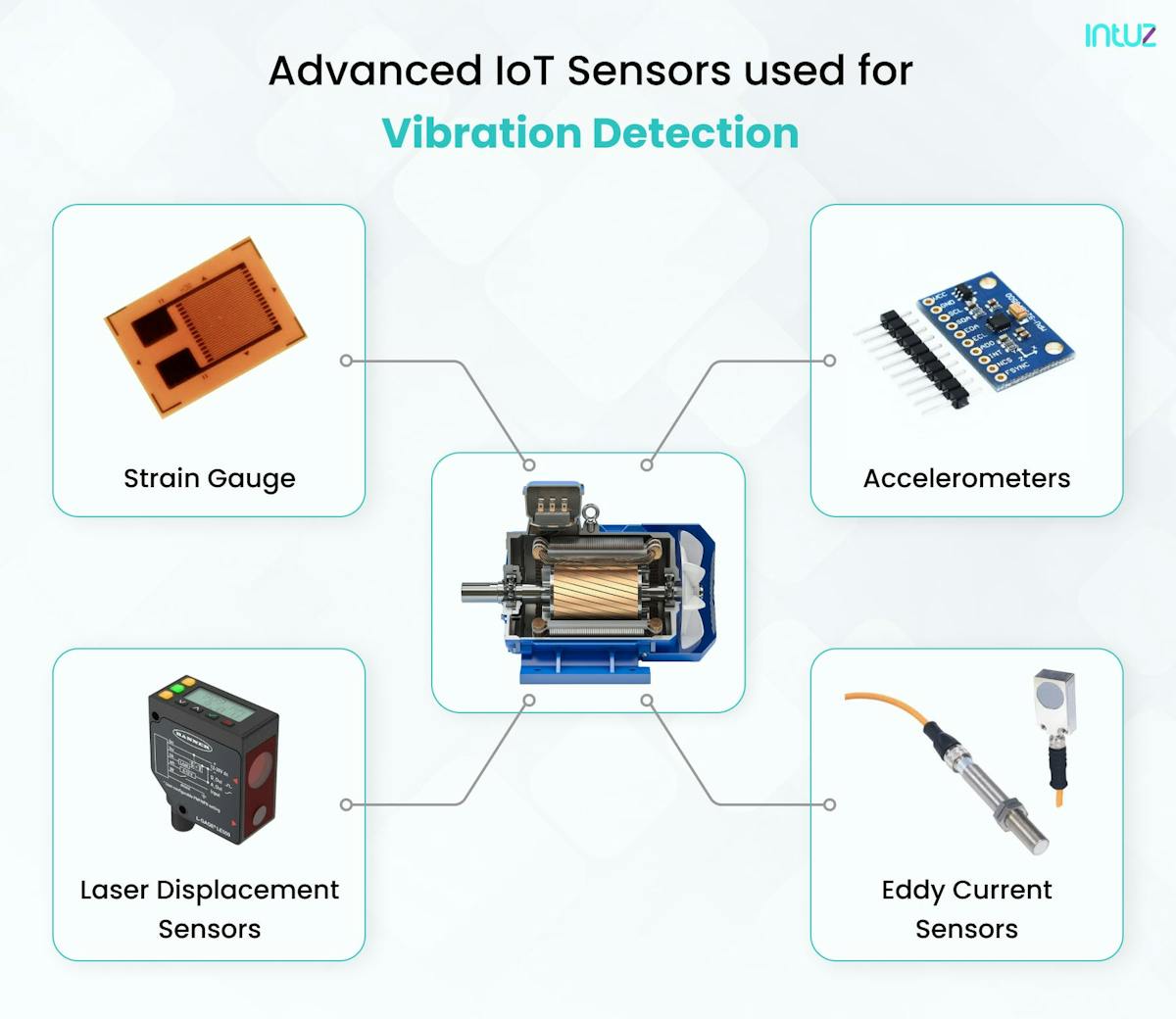
1. Accelerometers:
Accelerometers are the most commonly used sensors for vibration measurement. They are sometimes used with a gyroscope because they cover a white spectrum of vibration frequencies.
There is a further subcategory of accelerometers that includes piezoelectric and piezoresistive sensors. Both of these sensors are used for vibration measurement.
2. Eddy current sensors:
These sensors measure the current produced due to changing magnetic fields. A static, non-uniform field displacement that produces current is measured to measure vibrations.
3. Laser displacement sensors:
As the name suggests, laser displacement sensors measure changes in height, distance, and vibrations using a laser.
4. Strain gauge:
A strain gauge is used to measure the change in electrical resistance. They can be tricky to implement as they need electronics to convert the electrical resistance into a displacement value.
Eddy current and laser displacement sensors are the most costly among all the sensors. However, they are the most accurate too. On top of that, laser displacement sensors and eddy current sensors work in a contactless mode.
MEMS vibration sensors are also used to measure vibrations. However, their operations are difficult.
The IoT-based Vibration Diagnostics Process!
A systematic IoT vibration diagnostic process is necessary for continuously analyzing vibration and further ensuring the optimization of maintenance practices. Here is a brief overview of the process!
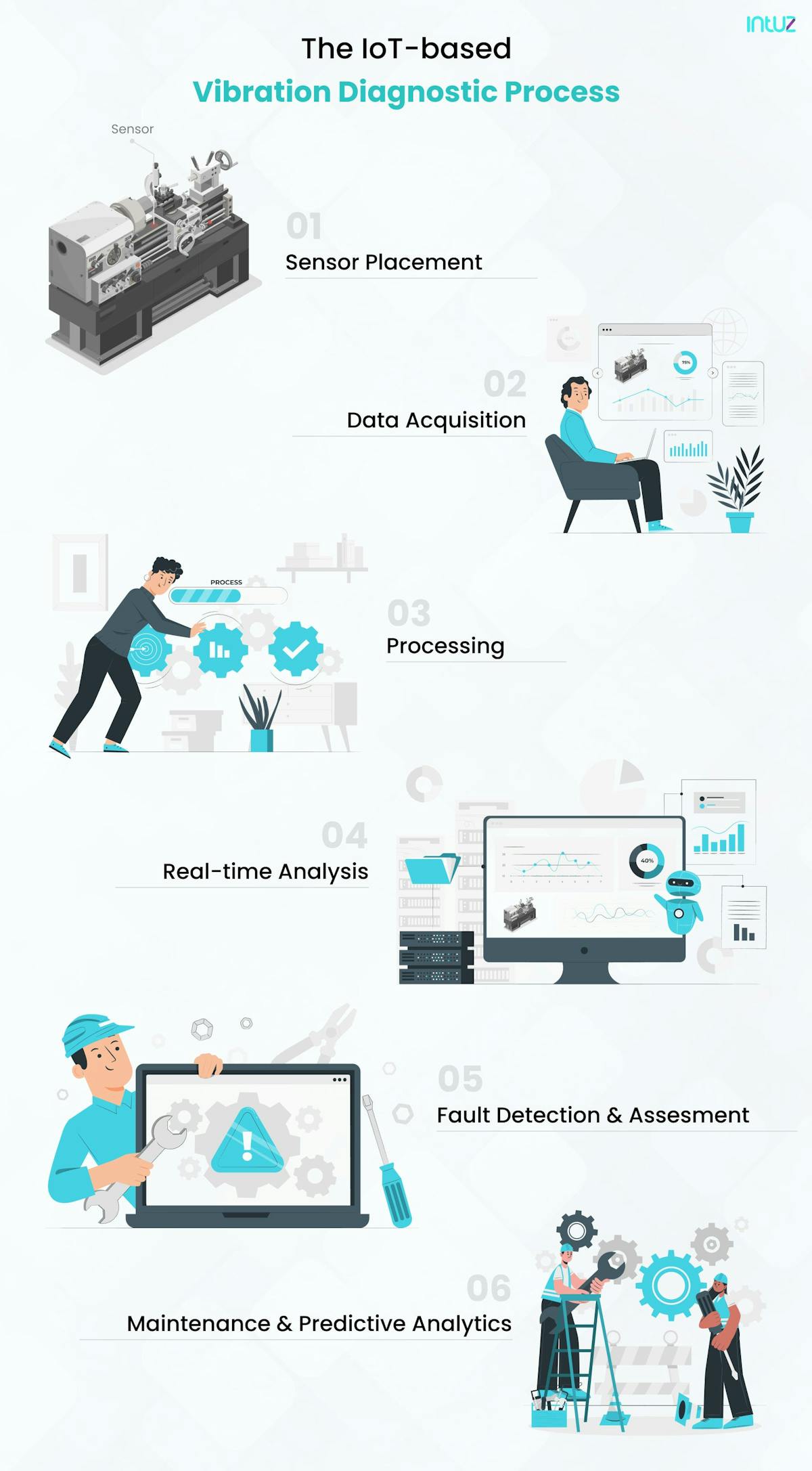
1. Sensor placement:
The first step is to install vibration measurement sensors on specific spots of the machine, such as motors, bearings, etc. These sensors can be of a single type, like an accelerometer, or a combination of all.
2. Data acquisition:
The placed or installed sensors can be used to capture vibration data and convert it into electrical signals for analysis. The analysis can be performed at the central IoT gateway or at the devices themselves (edge computing).
3. Processing:
The acquired electrical signal is processed to eliminate any noise or additional components using filtration, amplification, and digitization.
4. Real-time analysis:
The refined signal is analyzed using advanced analytics and ML algorithms in real time. These algorithms identify patterns and trends that allow you to detect potential faults. An example of such a mechanism is FTT. The Fast Fourier Transform algorithm produces an output where the vibration amplitude is represented as a function of frequency. This helps the analyzer understand the source of the vibration.
5. Fault detection and assessment:
The acquired results are compared with the threshold values of the vibrations, and faults are detected. Further, these faults are analyzed for criticality. It means it is decided if they must be dealt with immediately or during planned downtime.
6. Maintenance and predictive analytics
Maintenance teams are alerted to undertake the scheduled maintenance tasks based on the assessment outcome. Further, predictive analytics analyzes historical and current data and estimates the time for a specific part replacement or repair.
These steps are continuously performed to optimize the performance of the equipment.
Benefits of IoT-based Vibration Diagnostics
The use of IoT in the industrial landscape for vibration diagnostics yields several benefits!
1. Early fault detection
With the use of smart IoT sensors, vibrations can be detected continuously. The continuous data feed can be analyzed by AI to look for any abnormal changes. If any abnormal pattern is found, proactive fault detection measures can be taken, and counteracting solutions can be implemented.
2. Increased equipment reliability
With the help of proactive fault detection, issues can be detected and rectified before any major problems occur. Thereby boosting equipment reliability while delivering peak performance.
3. Reduced downtime and maintenance costs
As per statistics, advanced analytics data can predict machine breakdowns, reducing downtime by 30 to 50%. Regular access to vibration data from the machine helps prevent breakdowns and further reduce maintenance costs.
4. Enhanced safety for industrial workers
Working with properly maintained machinery daily boosts worker confidence. As IoT allows you to take proactive measures, you can boost workers' safety significantly.
A Complete Guide On IoT And Industrial Internet of Things [IIOT]
Learn MoreBrand Use Cases of IoT Solutions for Equipment Vibration Diagnostics
1. Rolls Royce
Rolls Royce is working on an engine health monitoring system to provide advanced and enhanced maintenance. This solution includes EVHMU, which is an engine vibration health monitoring unit.
The tool provides an advanced indication of a potential problem by analyzing thousands of data points in an engine’s operation. The solution also uses AI.
2. SNCF Railway
SNCF is a leading passenger and freight transport service provider. It has partnered with IBM to connect its entire rail system to IBM Watson IoT. The collaboration will allow SNCF to capture real-time data, including vibration data from the installed sensors. It will allow the company to anticipate repair needs and improve the security of its assets.
3. Bosch Rexroth
Bosch Rexroth is a prime developer of a cutting-edge and intelligent vibration analysis solution. The solution is a compact sensor package that uses modern-day sensor technology and edge analytics. Its remarkable features deliver valuable live vibration information to assist and ensure increased machine availability in agricultural facilities and other industrial applications.
4. Siemens
Siemens has introduced a smart condition monitoring solution, Sitrans SCM IQ. This state-of-the-art solution has a hardware part, the robust Sitrans MS200 multi-sensors. It can be attached to various machine parts, such as pumps, gears, compressors, etc., for temperature and vibration data capture. The solution uses AI and machine learning for anomaly detection in the data.
5. Schlumberger
Schlumberger’s i-DRILL Integrated Dynamic System Analysis Service is a solution that helps optimize the drilling process. With the solution, the users can avoid lost time by determining the root cause of the vibrations, inefficiencies, etc., before any major issue surfaces.
Explore Complete Guide on IoT in Predictive Maintenance!
Read NowConclusion
Based on the overall article and use cases, IoT is a pivotal technology that is not limited to only one industry sector. Almost every industry sector is using IoT to keep up with the competition.
With its increasing market and cutting-edge solutions taking over, it will be best for you to employ IoT in your business. And if you are ready to take your business forward with IoT, Intuz can be your perfect partner. Our top-notch IoT and AI solutions can help your business become a benchmark of excellence for other companies.
So, what are you waiting for? Book a free consultation with an Intuz IoT expert!