Table of Content
Simply out, Industry 4.0 refers to the new phase in the Industrial Revolution, which focuses primarily on interconnectivity, machine learning, real-time data, and automation. It is also characterized by integrating autonomous robots and machines with physical productions and operations to create more holistic and better-connected ecosystems.
This new industrial wave where machines infuse intelligence is an inevitable part of our lives. Look around yourself—and you will realize we cannot function without technology! From retail and healthcare to education and finances, there is a high level of dependence on it.
The pandemic has propelled the majority of businesses to drive digital transformation. However, they all face the same challenge - the need to stay connected and access real-time insights across products, processes, and people.
Naturally, Industry 4.0 is a step forward toward integrating smart technology in manufacturing with a focus on connectivity. Today, it is worth more than $4 trillion, as per KPMG, with the Internet of Things [IoT] market valued at 3.7 trillion.
Industry 4.0 - how it is impacting manufacturing
When the phrase "Industry 4.0" was first coined at Hannover Fair in 2011, there was no clarity on its impact on the industry as we know it. For instance, in 2018, the UK realized that embracing Industry 4.0 could unlock billions for them. However, they did little to prepare for this change, which required automation and other digital technologies.
But things soon changed. As more businesses became aware of the need for secure connected devices, global spending on IoT security went up to £1.5 billion. The UK subsequently invested £400 million in electric charging infrastructure.
Around the same time, telecom started to play a central part in Industry 4.0, opening up enormous opportunities for mobile connectivity in the manufacturing industry that later evolved into real-world applications of Industrial Internet of Things [IIoT] data capture.
The US currently uses digitalization to introduce groundbreaking research and commercialization of technologies such as semiconductors, materials and composites, flexible hybrid electronics, and clean energy in their manufacturing sector.
Are You Ready to Upgrade Your Factory with Our Industrial IoT 4.0 Expertise?
Contact Us NowA journey through industrial revolutions
It was no later than the 19th century when the world was first transformed by the Industrial Revolution with the introduction of steam engines. It represented the shift from farming to factory production in the US.
The second spanned from the 1850s to WWI and began with the introduction of steel, culminating in the early electrification of factories and setting up assembly lines for mass production. The third industrial revolution was when the world switched from analog and mechanical technology to digital technologies in the late 1950s to the late 1970s.
The Industry 4.0 trends are characterized primarily by Machine-To-Machine capabilities and IoT development process, involving the use of cyber-physical systems such as sensors to access large volumes of data that can be used by manufacturing units to automate complex tasks and improve process efficiencies.
Top things to know about Industry 4.0
Now that you have taken a glimpse at how the fourth wave of the industrial revolution came to be, let us explore six areas where it is contributing to their growth massively:
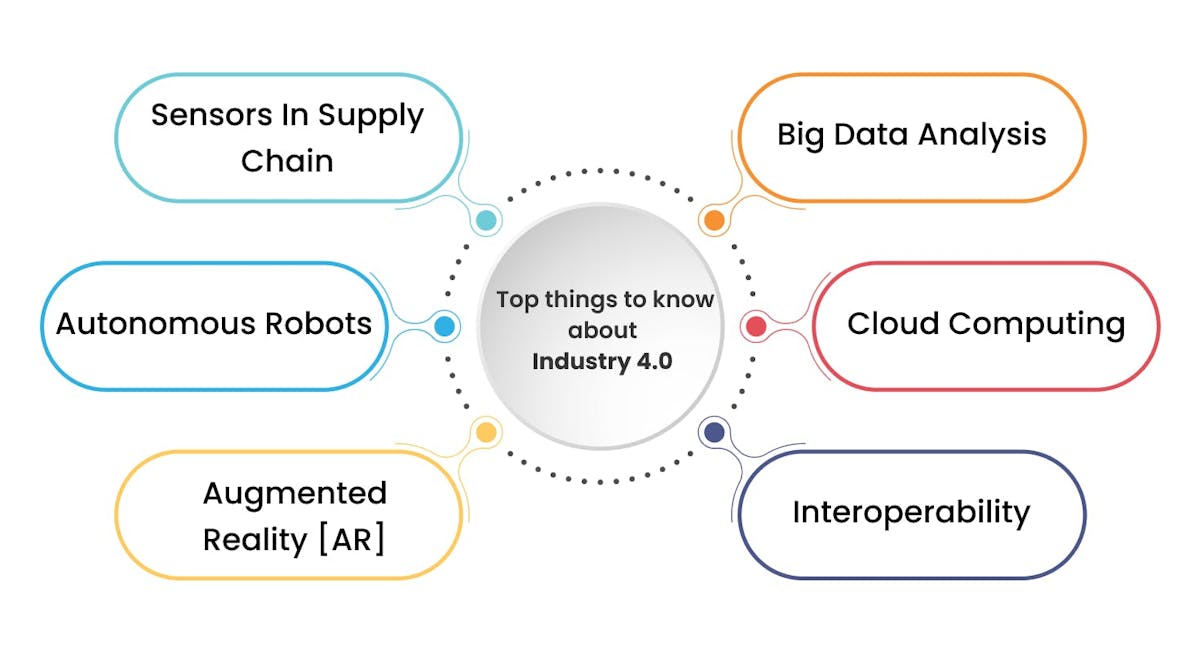
1. Sensors in the supply chain
Industrial IoT solutions deploy various sensors, such as RFID tags, within industrial systems and machines to collect real-time data about their condition or performance. Industry 4.0 runs on connected sensors that monitor processes and transmit readings.
This helps manufacturers study usage trends that can be further used to inform product development and improve after-sales service offerings.
Such smart sensors help in boosting operational efficiency, lowering production costs, and providing customer behavior insights. IIoT also has other use cases, such as asset management and tracking, that are possible due to the use of sensors.
2. Big Data analysis
This term refers to the complex process of gathering information such as customer preferences, market trends, unknown correlations, and so on.
Ever since Big Data entered the picture, the challenge is that there are too many digital touchpoints from which information has to be gathered, so there is a need to develop methods to best interpret the data.
The advent of Industry 4.0 has given birth to Big Data and analytics solutions, which are slowly changing how businesses use data to make better, smarter decisions. Machine learning models (such as statistical algorithms and predictive modeling) and data visualization are applied in the data analytics process.
3. Autonomous robots
Robots have been around for a while, but they can work faster and smarter in factories with better technology. It would not be surprising to see robots interacting with each other and adjusting their actions for every new product they produce in the future.
That way, instead of mass-producing a product incorrectly, manufacturers will be able to analyze each product and identify flaws early on through robots. This will not only lower production costs but also boost quality.
Another significant area where robotics is gaining prominence is collaborative robots, or cobots, designed to work safely around people, freeing factory workers from dangerous and repetitive tasks.
4. Cloud Computing
Data is being collected at a staggering speed in this day and age, making it impossible for manufacturers to handle it all manually. So with all the information they collect, it is necessary to have a cloud platform.
Industry 4.0 has made it possible for them to store and share massive amounts of data in real time. Now they can leverage scalable computing resources and storage space to capture and apply business intelligence to streamline manufacturing operations.
In 2021, manufacturers' global spending on cloud computing platforms is expected to touch $9.2 billion, as per an IDC report. A significant factor behind this adoption is operational centralization, so that information can be shared across processes in real time.
5. Augmented Reality [AR]
AR is the key to bridging the gap between the digital and physical worlds by superimposing virtual images on a physical object. We are sure you must have already come across AR-equipped devices such as smartphones and smart glasses.
In medicine, when a surgeon uses AR glasses during surgery, the glasses could overlay data from the patient's CT and MRI scans, giving a color-coded overview of significant blood vessels, nerves, and ducts. This provides the surgeon with the safest path to the region that needs invasion and minimizes the risk of complications during surgery.
In manufacturing, AR could enable workers to speed up the assembly process and improve decision-making. For example, AR glasses could be used to project data such as assembly guidelines, sites of possible malfunction, layouts, and so on.
Since this technology is relatively new, its current uses include selecting parts in a warehouse through robotics. Engineers hope to use it to help manufacturing units fix and make use of complex machinery conveniently.
6. Interoperability
This refers to the process of connecting cyber-physical systems—humans and smart factories interacting through IoT. With interoperability, manufacturers can effectively share information, error-free.
From self-driving vehicles to 3D prints, Industry 4.0 propels the manufacturing industry with new means of efficiency, reliability, and accuracy. This only gives us a glimpse of what is to come in the fourth wave.
IIOT and Industry 4.0 Use Cases
In simple words, Industry 4.0 also refers to smart manufacturing or IIoT, wherein multi-connected ecosystems are created by marrying physical operations with machine learning and Big Data. Here are a couple of use cases for Industry 4.0 results in smart manufacturing:
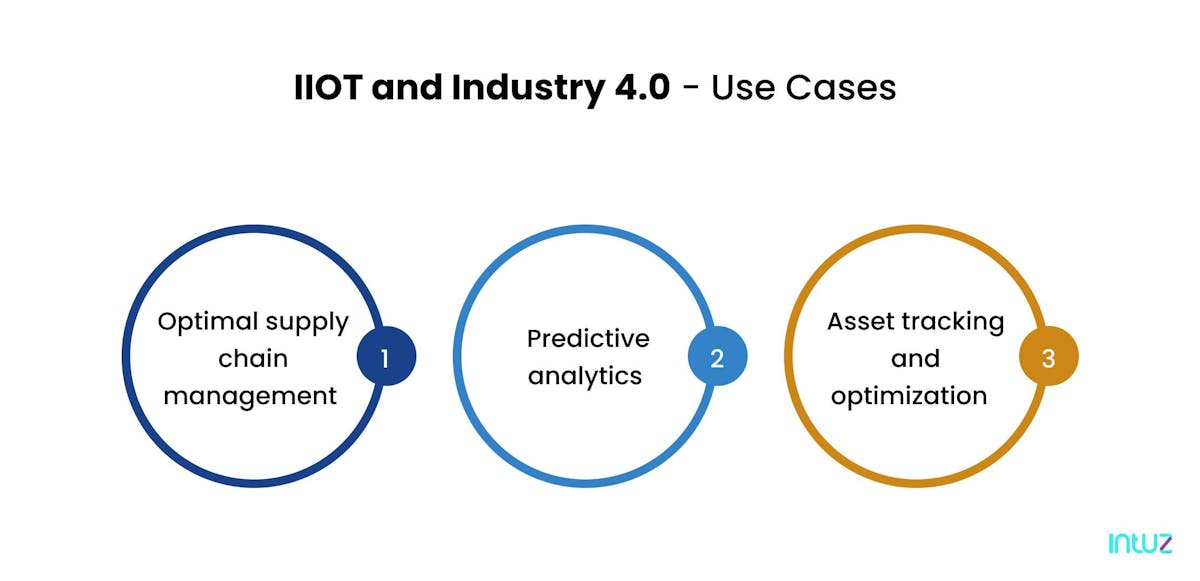
1. Optimal supply chain management
Thanks to Industry 4.0, businesses have more insight, more control, and better data visibility across their supply chains. By leveraging this power, they can deliver products and services faster and in a more efficient manner, gaining an edge over less-efficient competitors.
2. Predictive analytics
Using this, manufacturers can predict consumer problems before they arise. In the absence of IoT systems, identifying problems is often done manually and periodically, which takes longer and is prone to human error. Using predictive Industrial IoT solutions, maintenance is more streamlined and automated.
On the other hand, with predictive analysis, manufacturers can fix machinery that is on the verge of shutting down. That way, they can be proactive and pivot from preventive maintenance to predictive maintenance.
3. Asset tracking and optimization
Manufacturers are more efficient when keeping track of inventory, product quality, and logistical optimization opportunities in real time. If IoT technology has been deployed at a factory, manufacturers can enjoy the visibility of their assets worldwide. That way, tasks such as asset transfers, disposals, reclassifications, and adjustments can be streamlined and centrally managed in real-time.
Five ways in which Industry 4.0 benefits manufacturing businesses
Now that you have read this far, you will agree on how important it is to understand the fourth wave of the Industrial Revolution's impact. Industry 4.0 spans the entire product lifecycle and supply chain, from sales, inventory, and engineering to customer service.
But what is more important is to implement those changes in your business. Believe it or not, Industry 4.0 will help you:
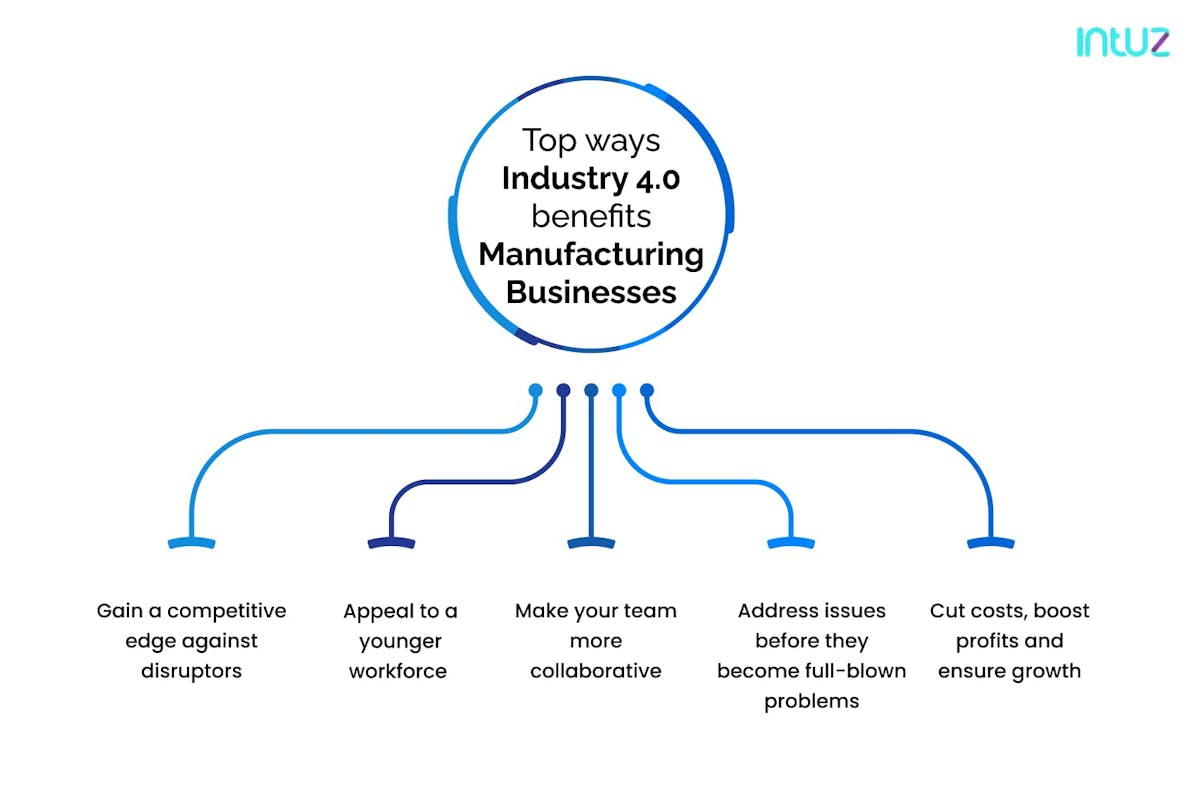
1. Gain a competitive edge against disruptors
Tech giants such as Amazon continue to optimize their logistics and supply chain management with IoT. This means your manufacturing business must also invest in technology to optimize your operations.
To remain competitive, you must have systems in place that allow you to provide the same level of service that your customers are getting from the likes of Amazon.
2. Appeal to a younger workforce
When companies invest in modern, innovative Industry 4.0 practices, they are more likely to attract and retain new workers from a young population. Every business wants that! Take advantage of this opportunity.
3. Make your team more collaborative
Industry 4.0 solutions help increase efficiency and boost collaboration among teams and departments, enable predictive and prescriptive analytics, and allow professionals such as operators, managers, and executives to better leverage real-time data and intelligence to make smarter decisions every day.
4. Address issues before they become full-blown problems
Predictive analytics, connected machinery, automation, and real-time data allow you to be more proactive toward solving potential maintenance and supply chain management issues. This ensures smooth operational efficiency as you do not allow your machinery or systems to shut down or be faulty for long without better planning.
5. Cut costs, boost profits, and ensure growth
All aspects of manufacturing and supply chain management can be optimized with Industry 4.0 technologies. With access to real-time data, you can make faster and better decisions, which will ultimately lead to increased efficiency and profitability of your manufacturing unit.
Situations where investing in Industry 4.0 is the right decision for your business
- You want to deploy a fully-integrated resource planning system that covers financials, inventory, and SCM
- You want your team to be better informed of all production processes
- You want to deal with system shutdowns and faults proactively
- Recruiting for vacant positions in your business is a challenge
- You want better efficiency and profitability for your business
- You want analytics to be more valuable and in real-time
- You want to deliver an optimal customer experience
- You need help in making sense of massive data sets
- You are in a highly competitive industry
- You want to improve your product quality
Modernize Your Manufacturing Operations with Custom Industrial IoT Solutions!
Explore SolutionsWrapping it up
Without a doubt, Industry 4.0 is the way to the future and is of tremendous significance in manufacturing. Businesses want access to up-to-date and relevant views of production and business processes. This is where Industry 4.0 comes in.
We already see factories becoming increasingly automated, where machines can analyze and communicate with each other. With this support, manufacturers on all levels will have more time on their hands to focus on other essential tasks.
Those who are delaying upgrading their businesses to new models will soon need to adapt and catch up as there is a high risk of becoming redundant in this competitive market. If you want to develop IoT Solutions for your business but need experts to do it for you, let us help you out.