Table of Content
The power plant market is primarily driven by increased electricity demand over the past decade, fueled mainly by a growing population and rapid industrialization and urbanization worldwide. This trend is expected to continue as usual in the years to come, with the need for electricity projected to propel market growth.
In 2020, the global market for power plants was valued at $1,345 billion. Today, it is predicted to reach $1,821 billion by 2030, growing at a CAGR of 3.2% from 2021 to 2030. These plants are used for converting heat energy into electric power for residential and commercial applications.
The curious case of coolants: Monitoring is paramount
Power plants that use recirculating cooling typically rely on a condenser circuit to cool down the water, which is then directed to a cooling tower. Coolant monitoring is necessary for many reasons, as it poses several challenges.
Firstly, if the coolant flow is insufficient, it can lead to a buildup of heat, damaging the equipment and decreasing the power plant output. Secondly, the cooling tower discharge can impact the environment, including nearby bodies of water.
Thirdly, coolant monitoring helps identify potential leaks or contamination, which could have safety implications for plant workers and the surrounding community.
Parameters to take note of in coolant monitoring
Thankfully, many fluid parameters such as coolant density, viscosity, temperature, pressure, color, pH, and turbidity play a critical role in the efficiency, safety, and environmental impact of power plant operations.
For instance, viscosity and pressure affect fluid flow rate and can impact plant yield, while higher temperature increases the heat transfer rate. On the other hand, color indicates impurities in the coolant, pH affects corrosion rates, and turbidity highlights the presence of solids in the fluid. Proper control and monitoring of these parameters can optimize power plant operations, reduce costs, and minimize environmental impact.
Reduce Downtime: Implement Smart Coolant Monitoring in Your Plant!
Let's Get StartedThe main challenges with coolant in power plants
Coolant plays a critical role in the efficient and safe operation of power plants. The following are the main challenges that one should know about:
1. Temperature fluctuations
Power plant heat exchangers are vital components that facilitate heat transfer between fluids. Temperature fluctuations can, unfortunately, affect their performance.
For example, if the temperature of the coolant is too low, it can form ice or other deposits on the heat exchanger, decreasing heat transfer efficiency. Similarly, if the temperature of the coolant is too high, it can cause it to expand thermally, leading to deformation or failure.
2. Pressure fluctuations
Such fluctuations are proportional to temperature variations, leading to challenges in maintaining the correct fluid flow rate and pressure and affecting the resourcefulness of the cooling system.
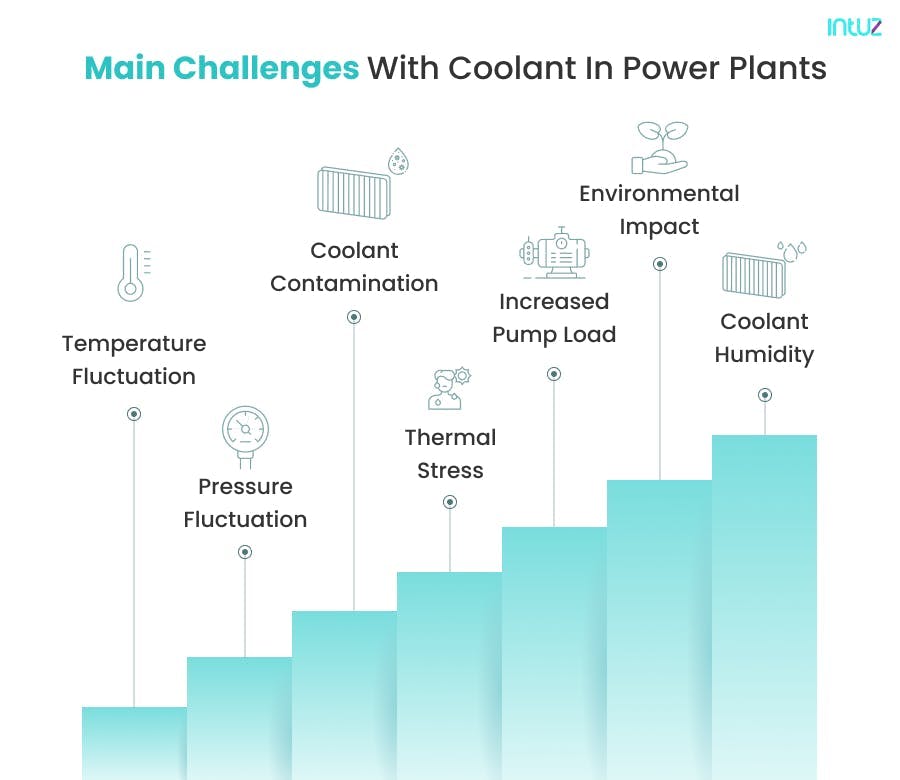
3. Coolant contamination
It can happen due to the buildup of contaminants such as dirt, debris, and minerals in the coolant system. This reduces the overall system productivity and increases the risk of equipment damage.
4. Thermal stress
Temperature fluctuations can cause thermal stress, deformation, cracking, and equipment failure. This is particularly true for components such as pipelines and heat exchangers exposed to significant thermal stresses.
Therefore, it is essential to control the temperature of the coolant to prevent thermal stress and ensure equipment longevity.
5. Increased pump load
The low viscosity of the coolant can increase the pump load, which invariably minimizes the capability of the power plant and increases unnecessary energy consumption. So it is vital to maintain the viscosity of the coolant and enable optimal performance of the power plant.
6. Environment impact
Changes in coolant density can affect the emissions of pollutants, such as nitrogen oxides and carbon monoxide. Monitoring the coolant density helps cut the negative environmental impact of the power plant and ensures compliance with regulatory standards.
7. Coolant humidity
The humidity of the coolant can impact the efficiency of gas turbines, as moisture can cause the metal surfaces of the equipment to rust and deteriorate. This disrupts the supply chain and causes business loss - in terms of money and credibility in the market.
Condition Monitoring Using IoT In Brewing And Distillation Industry
Read nowIoT-based solutions for coolant monitoring in power plants
IoT applications in the energy sector have garnered attention from consumers, businesses, and governments alike.
In addition to its numerous benefits to the electric power supply chain, IoT technology paves the way for smarter grids and promises unprecedented savings, improved security, and enhanced performance. Let us look at the different IoT solutions that make managing coolant in power plants a lot easier:
1. Advanced control systems
Such systems utilize advanced algorithms and sensors to continuously monitor and adjust coolant temperature and pressure in real time, empowering plant operators to quickly identify and respond to changes in coolant parameters.
Temperature control using IoT helps minimize the risk of equipment damage by deploying predictive maintenance features that can ascertain potential issues in specific parts of the reactor, such as heaters and transmitters before they become critical.
By analyzing data from sensors and other IoT sources, the maintenance teams can take proactive measures before equipment failure, resulting in downtime and power supply disruption.
Predictive maintenance also allows power plant operators to optimize maintenance schedules, condense the frequency of maintenance activities and minimize the impact of maintenance on plant operations. This can improve yield and shave off costs associated with maintenance activities.
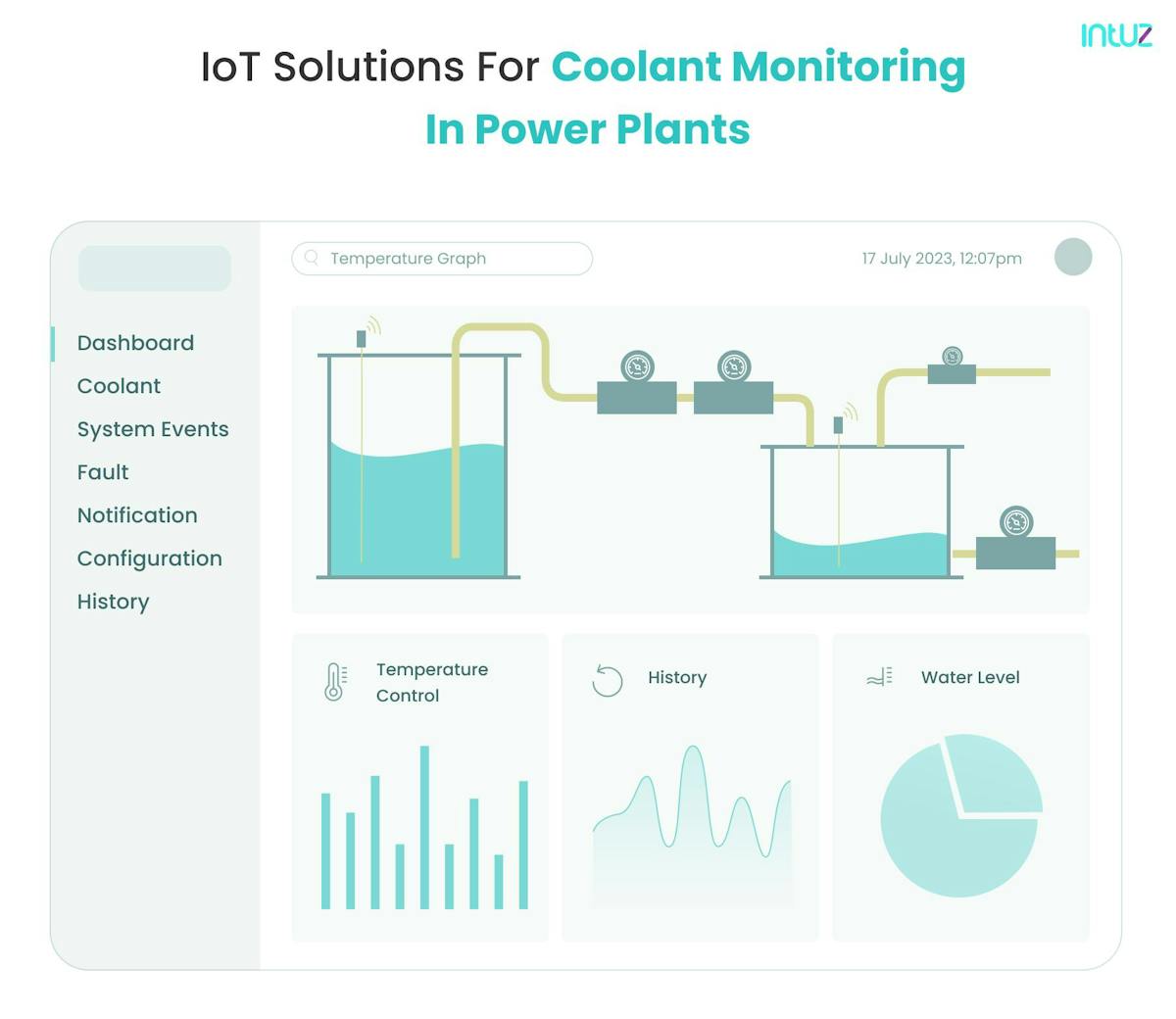
2. Cloud-based remote monitoring platforms
These platforms have become increasingly popular in power plant operations, enabling operators to monitor plant performance and coolant parameters in real-time from a central location - from anywhere.
These cloud-based platforms offer a centralized interface for monitoring coolant quality across multiple power plant locations. The coolant parameters can include coolant temperature, pressure, density, viscosity, pH, turbidity, and color.
The sensors installed in the coolant system of each plant location send data to the cloud-based platform, where it is analyzed and presented visually to the operators.
It can discover faults or changes in the coolant's color or thickness, enabling operators to implement remedial measures before the issue becomes critical. In addition, the platform can generate alerts and notifications, allowing operators to respond quickly to potential problems.
3. Wireless sensors and actuators
These IoT tools can measure and control parameters such as Total Dissolved Solids (TDS), pH, and coolant viscosity, allowing for more precise and accurate control of coolant quality.
By undertaking coolant monitoring using IoT, operators can quickly find out changes in coolant quality and mitigate the problem before issues become critical. This helps minimize the risk of equipment damage or failure.
In addition to measuring coolant parameters, wireless sensors can be used to investigate abnormalities in the system, such as bearing wear or misalignment. Vibration sensors, for example, can ferret out these abnormalities, allowing operators to make things right before they lead to coolant leakage or pump failure.
Wireless sensors and actuators can also control other aspects of power plant operations, such as coolant flow rate or valves and pumps' operation. Wireless sensors and actuators can help improve plant efficacy, reduce downtime, and enhance safety by providing real-time data and control.
4. Flow meters
These are used to monitor the coolant flow rate and detect any blockages or leaks in the system. By providing real-time updates on a central dashboard, operators can quickly pinpoint and respond to issues, minimizing the risk of equipment damage.
Flow meters work by measuring the flow of coolant through the system. They are installed at various points throughout the coolant system, such as at the inlet and outlet of heat exchangers, to monitor flow rates and bring to light any changes that may indicate a problem.
For example, a sudden drop in flow rate may indicate a blockage in the system, while an increase in flow rate may indicate a leak. These can also be used to optimize coolant flow rates, improving the efficiency of the cooling system and trimming energy consumption. By providing real-time data on coolant flow rates, operators can adjust flow rates to maintain optimal performance and reduce waste.
In addition, flow meters provide valuable data on coolant quality, such as the presence of contaminants or changes in viscosity. This information can be used to optimize coolant treatment strategies and improve overall system performance.
5. IoT-based dehumidifiers
They are a relatively new addition to power plant operations, providing an automated solution for managing humidity levels and preventing corrosion. These dehumidifiers are equipped with sensors and IoT connectivity, allowing for remote monitoring and control of humidity levels.
Humidity can be a significant issue in power plant operations, particularly in areas with high ambient humidity. High humidity levels result in corrosion and decreased equipment efficiency, resulting in higher maintenance costs and decreased output.
To address this issue, power plants have traditionally used dehumidifiers, which are manually operated and require regular maintenance. IoT-based dehumidifiers offer an automated solution to this problem, enabling remote monitoring and control of humidity levels.
These dehumidifiers are equipped with real-time sensors that measure humidity levels and adjust dehumidification as needed to maintain optimal levels. This ensures that humidity levels are consistently maintained at optimal levels, preventing corrosion and minimizing maintenance costs.
In addition, IoT-based dehumidifiers provide valuable data on humidity levels and dehumidification performance, allowing operators to optimize dehumidification strategies and scale back energy consumption.
By providing real-time data on humidity levels and dehumidification performance, operators can adjust dehumidification schedules and settings to maintain optimal performance and reduce energy waste.
Cutting-edge Industrial IoT Solutions and Development Services Company
Explore the servicesOver to you
There is no doubt that IoT-based solutions in power plants offer several benefits, such as enhanced efficiency, shortened downtime, and predictive maintenance in the power plants. However, several challenges are associated with IoT implementation in this context.
That mainly includes concerns around data security, interoperability, system reliability, and scalability, integration with existing processes, and cost considerations.
Power plants must, therefore, carefully plan and execute IoT deployment while addressing these challenges to achieve the maximum benefits of IoT technology and ensure the ROI justifies this investment.
Book a Free 45-minute Consultation with Our IoT Experts Today! Get a customized roadmap and strategies to leverage IoT for coolant monitoring for your power plant.